Rockwell Automation fait rimer connexion et action
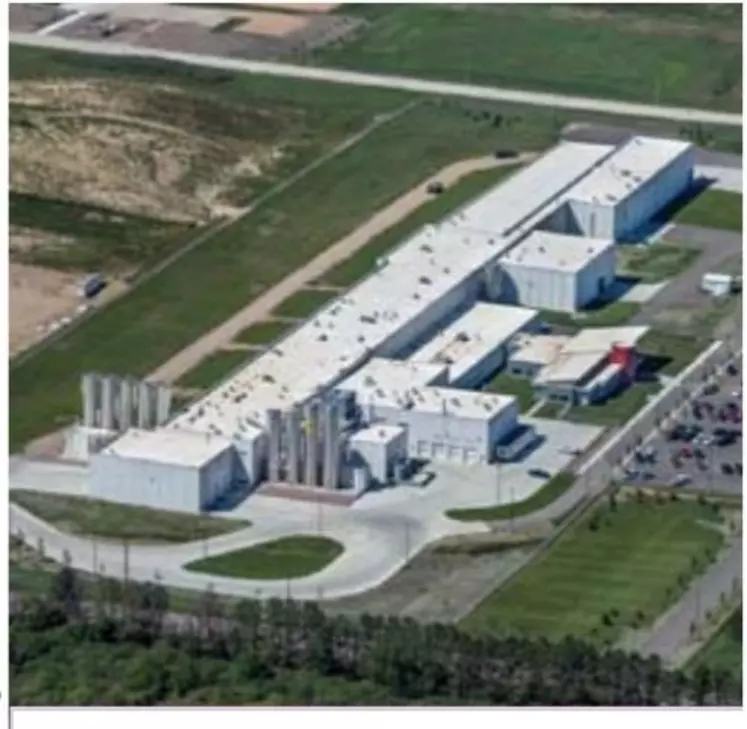
> Vue aérienne de « l'usine intelligente » de Bel dans le Dakota du Sud.
Rockwell Automation peut enfin communiquer sur « l'architecture intégrée d'automatismes » qu'il a déployée dans la nouvelle usine de Mini Babybel® aux États-Unis dans le Dakota du Sud, en passe d'atteindre l'objectif de 10 000 tonnes de fromage par an. C'est une « usine intelligente », organisée autour d'une infrastructure de communication EtherNet/IP, fonctionnant 24 heures sur 24 et 7 jours sur 7. Le spécialiste en informatique et automatisation a obtenu l'accord de Bel pour en faire une vitrine de son savoir-faire. Bel voulait faire de sa quatrième ” usine de Mini Babybel un outil particulièrement réactif, jusqu'à la gestion de l'énergie. Il l'a dotée de technologies de pointe, y investissant 144 millions de dollars (soit 113 millions d'euros).
“ Nous voulons [leur] permettre d'avoir les bonnes informations au bon moment
Pour la partie automatismes, le groupe français a eu affaire à des experts et commerciaux de Rockwell Automation en France, ainsi qu'au directeur de la branche française Gilles Pacaud. Ceux-ci ont travaillé avec les équipes locales de l'équipementier américain et des techniciens locaux connaissant déjà ces solutions, afin de respecter les pratiques et réglementations américaines. Rockwell Automation a accompagné d'autres fournisseurs français ou européens dans les domaines du process, de la mécanisation et du conditionnement. Il s'agissait de mettre en place des standards, des équipements informatiques jusqu'aux images devant apparaître sur les écrans. Les standards de programmation facilitent la maintenance. « Si un capteur se dérègle ou qu'une cellule est en arrêt, nos techniciens trouvent facilement les informations qu'ils souhaitent dans les programmes et peuvent intervenir plus rapidement », explique Christian Villedieu de Torcy, du département ingénierie de Bel. Chaque zone de l'usine a son automate de sécurité, relié au réseau Ethernet/IP ; elle peut être arrêtée indépendamment des autres.
Participer à l'usine française du futurRockwell Automation intervient aussi de façon plus ponctuelle. Le spécialiste de l'automatisation vient de mettre en place, dans des usines européennes alimentaires et pharmaceutiques, un nouveau système de guidage (iTrak) dissociant plusieurs mobiles d'une même chaîne. En France, le spécialiste de la connexion et des automatismes offre aux entreprises industrielles de tous secteurs le pouvoir de multiplier les produits grâce à l'ingénierie collaborative et au fonctionnement modulaire ; de réduire leurs coûts maintenance en simplifiant les architectures de contrôle ; de faciliter les diagnostics et d'anticiper les pannes. Une technologie de communication, Io-Link, accélère par exemple le signal d'un capteur en détectant les dérives.
« Nous voulons permettre aux bonnes personnes d'avoir les bonnes informations au bon moment afin de prendre la bonne décision », a introduit le directeur général Gilles Pacaud à Paris devant la presse le 10 décembre. Jérôme Poncharal, « architecte solutions », a également montré comment la connexion permet aux industriels d'utiliser à meilleur escient leurs équipements et de gérer leurs risques de toutes sortes, de la perte financière jusqu'à l'atteinte à la réputation de l'entreprise.
Tous les niveaux de commande et d'information sont reliés dans une « entreprise connectée », via la technologie Internet, Ethernet et Cloud computing. L'intérêt est de tirer parti au plus vite des informations historiques et immédiates. C'est l'optimisation portée au niveau de l'entreprise, après l'optimisation des automatismes et de la production d'une usine. Cela demande de surmonter une contrainte qui est celle de l'infrastructure : le réseau doit être commun et surtout sécurisé. En matière de convergence Ethernet, Rockwell travaille en partenariat avec Cisco.