Une fabrique d'aliments à la ferme d’exception pour 700 truies et la suite
La fabrique d’aliment à la ferme réalisée par Marlène et Mathieu Bourveau fera sans doute référence pour longtemps grâce à sa cohérence et à la qualité des équipements choisis.
La fabrique d’aliment à la ferme réalisée par Marlène et Mathieu Bourveau fera sans doute référence pour longtemps grâce à sa cohérence et à la qualité des équipements choisis.
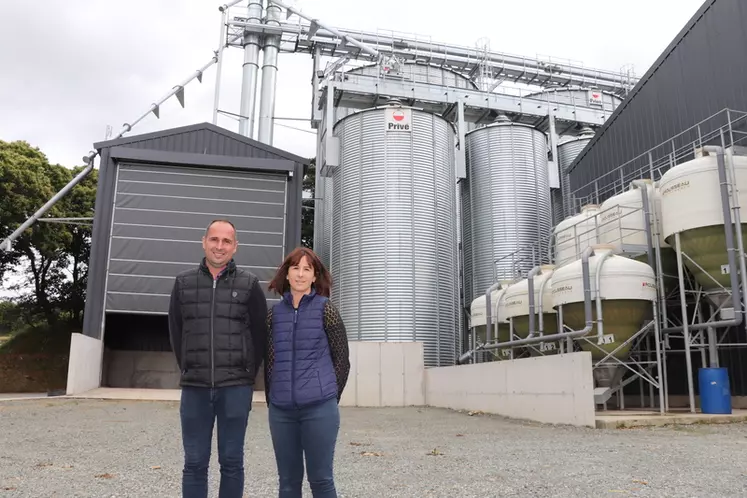
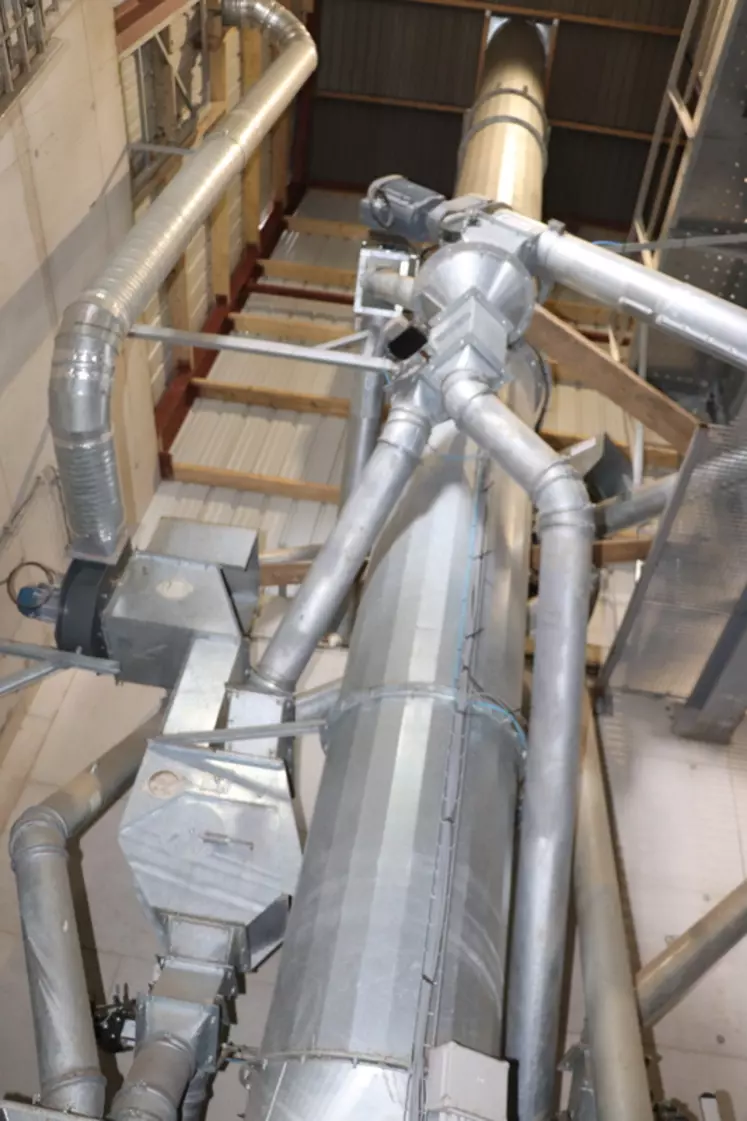
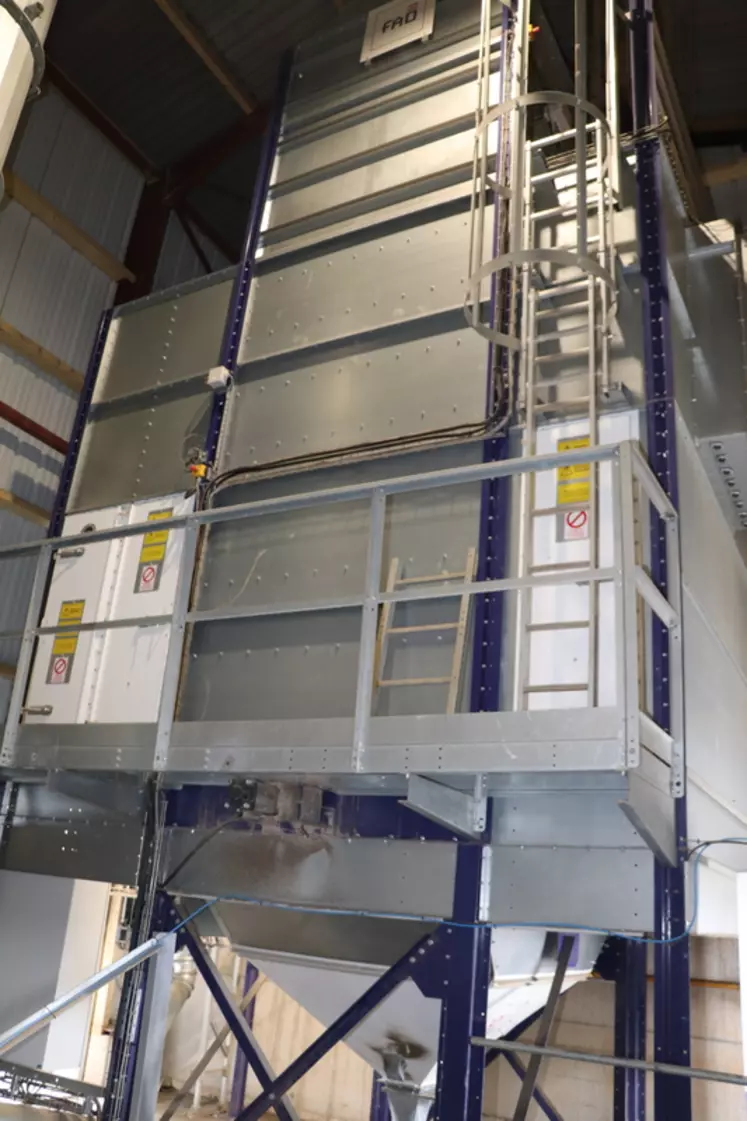
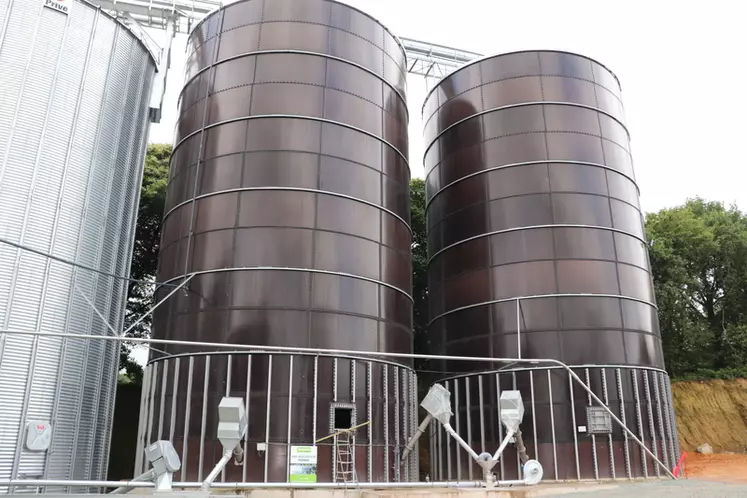
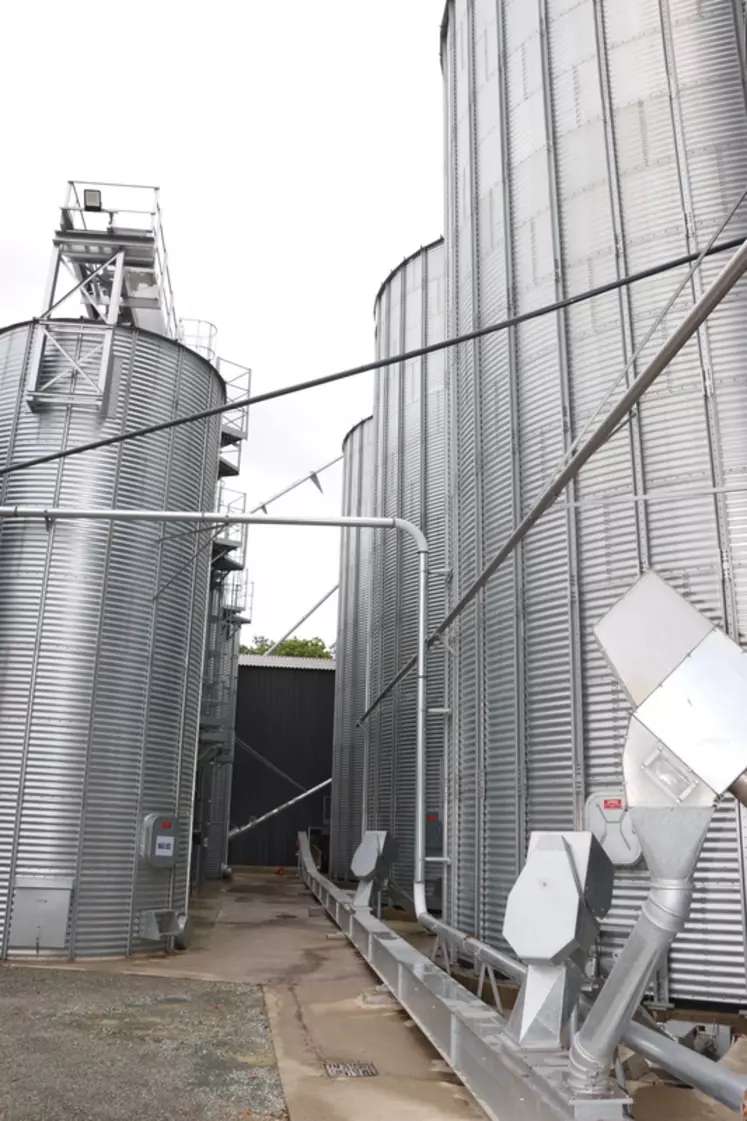
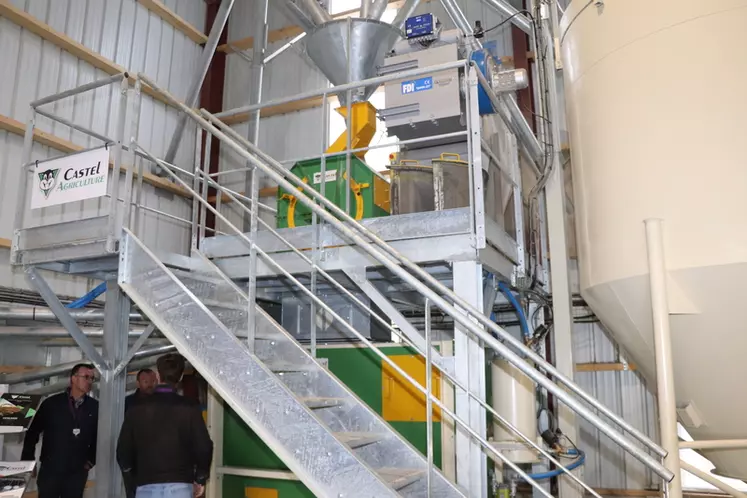
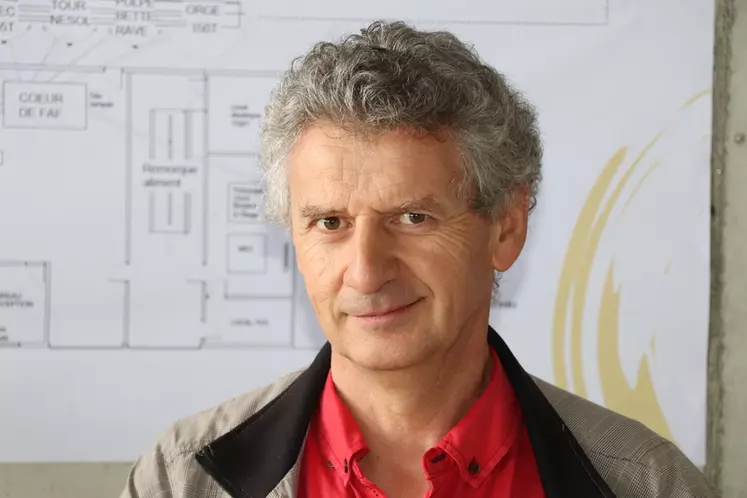
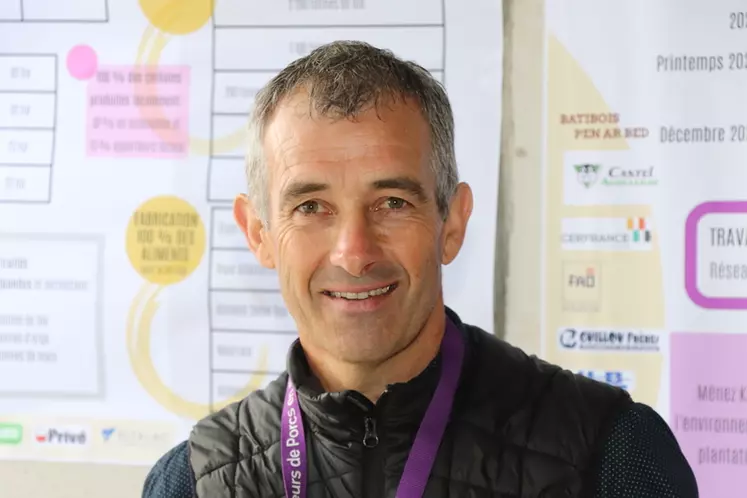
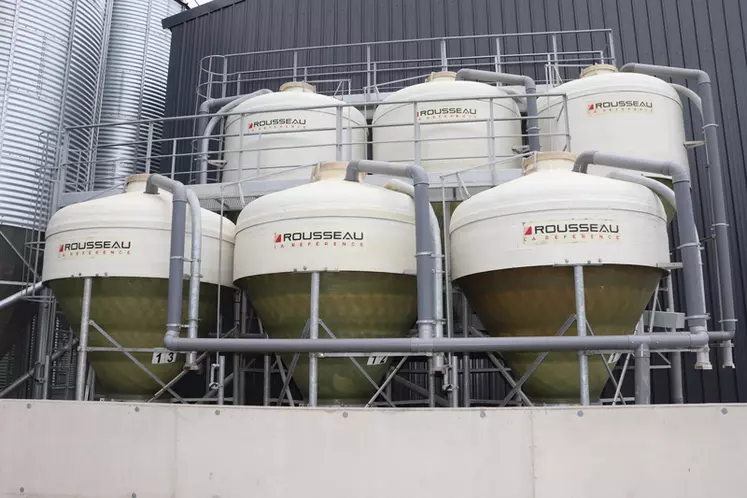
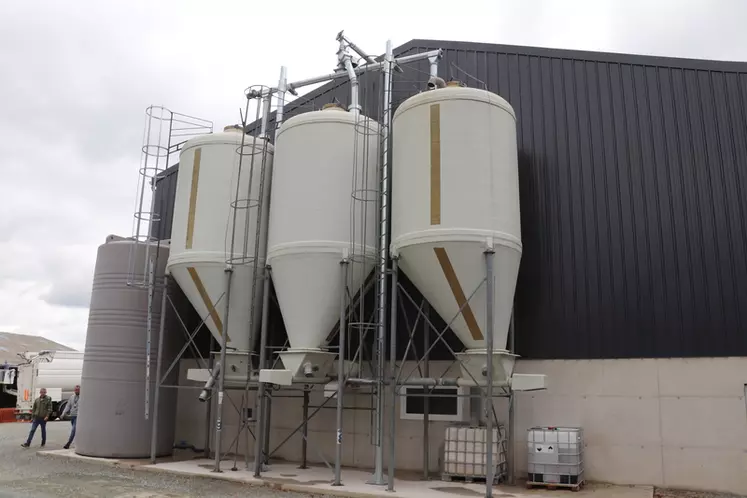
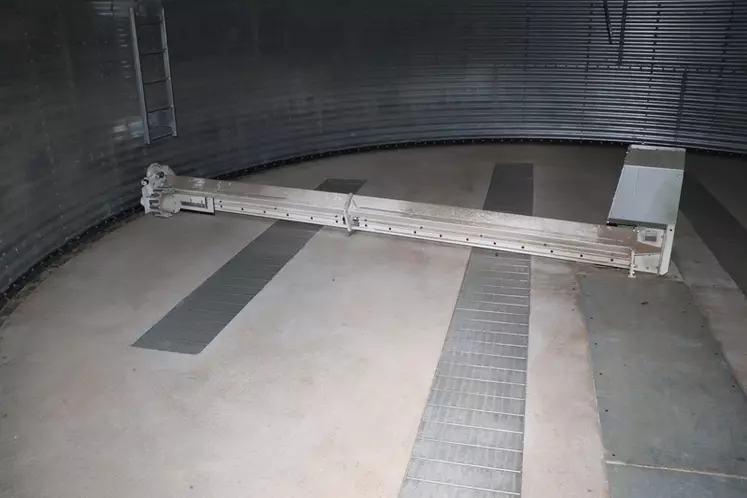
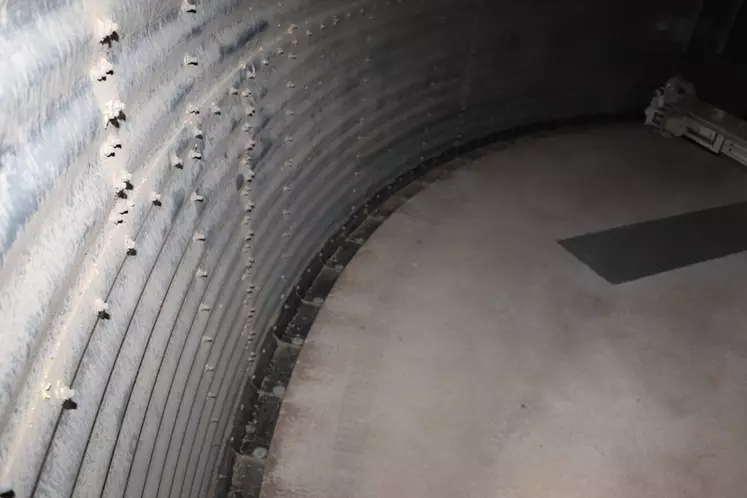
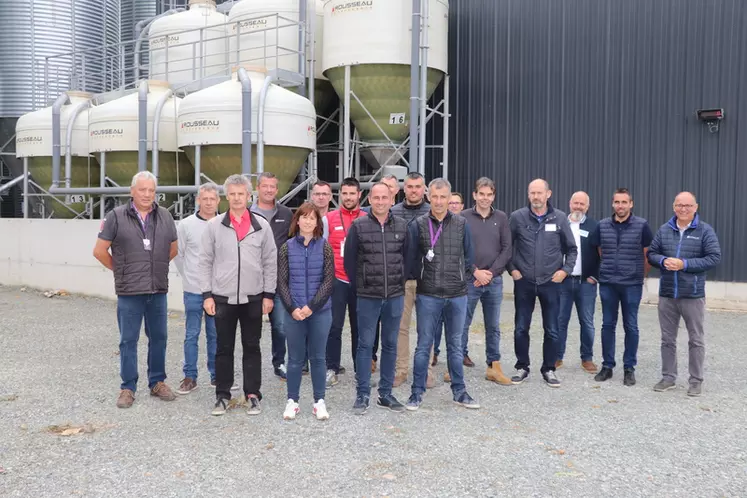
Avec leur nouvelle fabrique d’aliment à la ferme composée de 6 500 tonnes de capacité de stockage des matières premières, d’une unité de réception des matières premières, d’un ensemble broyeur-mélangeuse, d’une présoupe et d’une machine à soupe pour 7 500 tonnes d’aliment produits chaque année, Marlène et Mathieu Bourveau se sont donné les moyens d’assurer l’autonomie alimentaire de leur élevage de 700 truies naisseur-engraisseur pour longtemps.
Et malgré le montant de l’investissement qui pourrait paraître élevé (1,7 million d’euros, présoupe et machine à soupe incluses), les coûts de fabrication sont très compétitifs : « de 29 euros par tonne d’aliment fabriqué pendant les sept premières années, ils descendent à 14 euros par tonne après 15 ans d’activité, quand les installations sont amorties », calcule Thierry Lahaye, technicien Faf au groupement Evel’up.
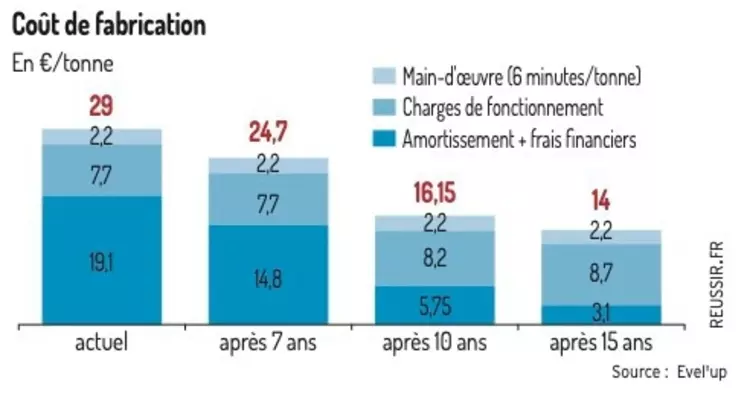
Des chiffres qui sont dans la moyenne des références élaborées par le groupement pour ce type d’installation. Et qui permettent d’améliorer le coût de revient du kilo de croît par rapport à de l’aliment complet : en 2021, Evel’up a calculé un écart de prix moyen d’aliment entre la Faf et les aliments du commerce (farine) à 32 euros la tonne.
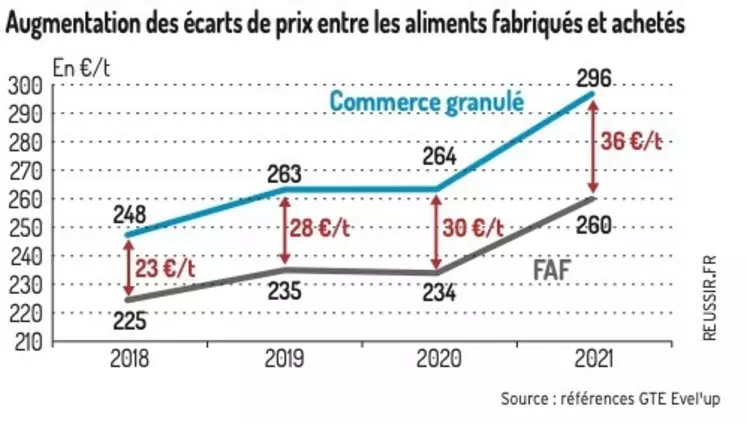
Ce qui fait dire à Mathieu que « fabriquer nos aliments fait partie intégrante de notre métier ». Par ailleurs, l’autonomie alimentaire de l’élevage est assurée à 100 %, à partir des céréales cultivées sur les 230 hectares de SAU de l’exploitation et chez les voisins. « Les trois quarts sont collectés dans un rayon de 15 km. » Un argument environnemental qu’il a su mettre en exergue lors de la constitution de son dossier, au même titre que l’insertion paysagère des installations. « Nous sommes sur un site classé qui nous a imposé de tenir compte de l’insertion paysagère des installations, en travaillant avec la Dreal et l’architecte des bâtiments de France. » Le résultat est bluffant. On a peine à imaginer une installation d’une telle envergure quand on circule sur la route qui longe le site. Les abords extérieurs ont été aménagés, avec des haies champêtres et des arbres, protégés par des paillages naturels (copeaux ou feutre biodégradable, plastique interdit !). Par ailleurs, l’entrée de la fabrique est indépendante de celle de l’élevage, pour des raisons de biosécurité. « Les camions de matières premières ne passent pas dans l’enceinte de l’élevage. » À noter cependant que les contraintes environnementales n’ont pas impacté ses choix techniques. Ces choix tiennent compte du temps de travail consacré à la fabrication des aliments (un mi-temps prévu), de l’optimisation des coûts d’investissement et de fonctionnement, et de la possibilité de diversifier les formules en fonction du prix d’intérêt des matières premières disponibles. L’installation est également agréée OS (organisme stockeur), ce qui permet de facturer directement le vendeur ou l’acheteur de céréales sans passer par un tiers. La porte ouverte organisée par les fournisseurs et Evel’up le 24 juin dernier a permis de découvrir cette installation et de détailler les équipements qui la composent.
Fabriquer nos aliments fait partie intégrante de notre métier
1-Une réception des matières premières pour des gros volumes
Après avoir passé sur le pont-bascule, les camions se positionnent devant la fosse de réception de 50 m3, pour une capacité totale de 80 tonnes. Elle est suspendue afin de supprimer totalement les risques d’infiltration d’eau. Les matières premières sont reprises par une grosse vis de 273 mm de diamètre permettant un débit de 85 tonnes par heure. Deux élévateurs dits « à jambe ronde » sont constitués d’un gros tube installé verticalement (35 mètres de haut). Ils contiennent une sangle entraînée par un moteur. Sur cette sangle sont installés des godets. Ces élévateurs peuvent à la fois réceptionner les matières premières, les transférer d’une cellule à l’autre ou les envoyer vers le séchoir fonctionnant au gaz. Cet équipement est essentiellement utilisé pour le blé et l’orge (capacité 200 tonnes par jour), parfois insuffisamment secs à la récolte (nous sommes dans le Finistère !). « Nous séchons aussi 200 tonnes de maïs chaque année pour les aliments des truies en maternité et des porcelets distribués à sec. » La réception comprend également un nettoyeur à cascade pour le dépoussiérage des grains, dans lequel un flux d’air montant croise le flux des grains descendant. Le flux d’air entraîne ensuite les poussières vers un silo annexe.
2-Du stockage en sec et en humide
Deux silos tour permettent de stocker au total 3 000 tonnes de maïs humide inerté. Leur diamètre (10,2 mètres) est plus élevé que les modèles standards, afin de compenser une hauteur limitée à 18 mètres pour l’insertion paysagère. Le fournisseur (Vitalac) a également dû trouver des silos marron en République tchèque, la couleur bleue étant interdite par l’architecte des bâtiments de France. Le cône de reprise en Inox est enterré sur 5 mètres. Pour éviter les infiltrations d’eau, un puits de 6 mètres de profondeur a été creusé. Il est relié à des drains posés sous la pointe des cônes. Les céréales sèches (blé et orge) sont stockées dans trois cellules extérieures de 1 100 tonnes chacune. « La solution extérieure est moins chère à l’achat que des cellules sous hangar », souligne Mathieu Bourveau. Leur étanchéité en partie basse est assurée par une cornière plastifiée posée sur le socle en béton (Privé). Les cellules sont équipées de vis racleuses sur fond plat. Pour la ventilation des grains, l’air passe dans des caniveaux grillagés, faciles à nettoyer entre deux récoltes. « La solution d’un venticône diminue le volume de stockage. Et surtout, elle coûte très cher pour des cellules d’une telle capacité (9,8 mètres de diamètre). » L’éleveur a également fait installer six cellules de travail à cône 60° (deux de 150 tonnes pour le blé et l’orge, quatre de 65 tonnes pour le tourteau de soja, le maïs sec, le tourteau de tournesol et la pulpe de betterave). « Cette installation est évolutive. Je peux installer de nouveaux silos si de nouvelles matières disponibles sur les marchés peuvent diminuer le coût des formules. » Six silos polyester de 5 à 8 m3 assurent le stockage des minéraux. « J’ai choisi de travailler avec des CMV 3 à 5 % plutôt que des COV 1 % auxquels il faut ajouter le phosphate, le carbonate et les acides aminés, pour des raisons de simplicité et de réduction du temps de travail », explique l’éleveur.
3-Un cœur de Faf à 3,5 tonnes par heure
Le cœur de Faf est composé d’un broyeur à marteau de 45 kW et d’une mélangeuse de 2 000 litres permettant des fabrications d’une tonne d’aliment, pour un débit moyen de 3,5 tonnes par heure. La mélangeuse est équipée d’une rampe à huile. Elle reçoit directement les minéraux, la précision de pesée étant suffisante pour ces petites quantités. La finesse de mouture peut varier selon la vitesse du broyeur. Les complémentaires au maïs humide (nourrain 70 %, croissance 50 % et finition 45 %) sont stockés dans des silos proches du local machine à soupe. La machine à soupe sert uniquement à la préparation des mélanges complémentaires + maïs humide, préalablement dilué dans une présoupe. Elle envoie ensuite les soupes vers trois cuves de distribution situées à proximité des bâtiments d’élevage. Un transfert pneumatique enterré assure le convoyage des aliments truies et porcelets distribués à sec vers des silos situés à l’élevage, à une centaine de mètres de distance.
Repères
Les matières premières utilisées (juin 2022)
« Un projet mûrement réfléchi »
Thierry Lahaye, technicien Faf Evel’up
« Mathieu a intégré dès son installation en 2019 le projet de construire une fabrique d’aliment à la ferme afin de prendre son prix en compte dans le projet global. L’objectif principal était l’autonomie alimentaire de l’exploitation, ce qui a un sens économique évident. Evel’up l’a accompagné dans la conception du projet et les choix des équipements. Le stockage extérieur, le nombre de cellules, le choix d’utiliser du CMV plutôt que du COV… ont été décidés en fonction de leur intérêt technique et de leur coût. L’implantation des installations a été étudiée pour qu’elle soit évolutive : des emplacements sont prévus pour ajouter si besoin des cellules et un silo tour. La Faf a également un sens environnemental. Elle contribue à la baisse du bilan carbone de l’exploitation dans la mesure où elle valorise les céréales produites localement. Elle limite aussi le transport des matières premières et l’énergie nécessaire pour sécher le maïs. Enfin, le travail réalisé par Mathieu et une bonne collaboration avec les services administratifs lui ont permis de concevoir une Faf qui s’insère discrètement dans le paysage sans perdre de son efficacité technique. »