Œnologie
Sous le carton des BIB
Loin d’être anodine, la fabrication des BIB réclame une grande technicité pour répondre à des contraintes de neutralité sensorielle, de sécurité alimentaire et de résistance mécanique. Petit tour de l’autre côté du miroir, dans l’usine Smurfit Kappa d’Epernay.
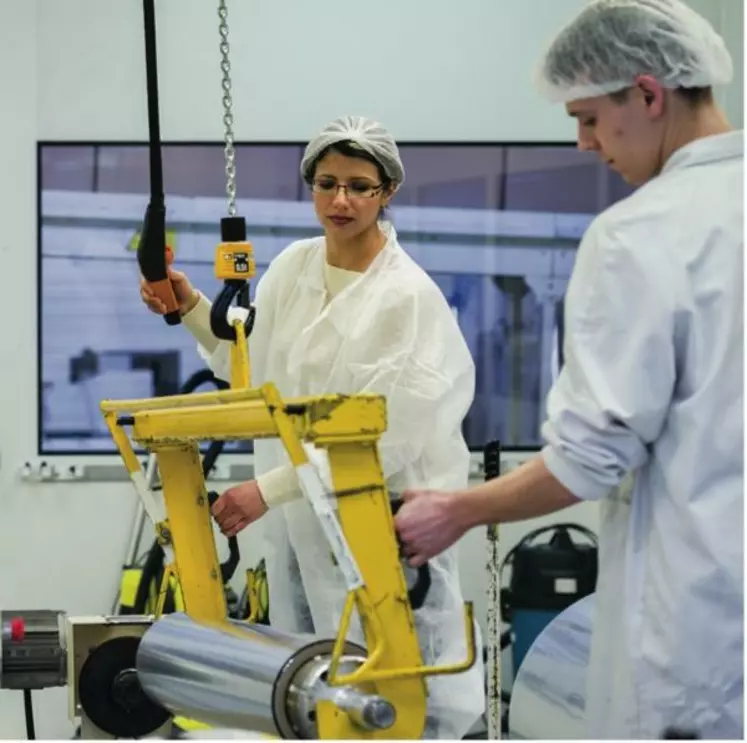
l’un des films extérieurs
de l’outre du BIB, constitué
d’un sandwich de deux types
de plastiques, dont l’EVOH
responsable de l’étanchéité aux gaz et de la résistance mécanique.
Une banale poche en plastique, l’outre des BIB ? Avant de mettre les pieds dans une usine telle que celle de Smurfit Kappa d’Epernay, on pourrait le croire. Une fois avoir constaté la complexité de la composition des films plastiques, leur préparation, leur assemblage et leur conditionnement, on y croit subitement un peu moins.
Une ligne de confection de 20 m
Une fois les inévitables surchaussures, charlotte et blouse enfilées, formalités propres à l’intrusion dans une usine certifiée ISO 9001, et bientôt 22 000 (agrémentée du PAS 230), place à la partie opérationnelle. Quatre bobines de film plastique, fabriqué par un prestataire, sont déroulées sur la vingtaine de mètres qu’occupe une ligne de confection. En premier lieu, les films sont assemblés deux à deux par simple électricité statique. Le premier sandwich est d’abord percé au niveau du robinet, le goulot y est ensuite soudé, puis c’est au tour du robinet Vitop® (ou sa version compacte), fabriqué dans une usine du groupe en Italie, d’être positionné. Le second sandwich, indemne, rejoint le premier et leurs bords sont enfin soudés. La soudure est un point-clé de l’élaboration, et depuis peu Smurfit Kappa a développé une technique permettant d’arrondir les angles de la poche. “ Ce détail peut paraître insignifiant ”, fait remarquer Dominique Gessat, directeur de l’usine, “ mais cette soudure arrondie permet d’éviter que les angles de l’outre soient malmenés lors de son encaissage. ” Un prédécoupage plus tard, et des petites mains rangent soigneusement les bandes dans des cartons.
Sandwichs multicouches
Impossible de le voir sans détenir un microscope électronique, mais une poche de BIB fabriquée ici est en fait un sandwich multicouche, composé de deux types de films. “ Le premier film, en contact direct avec le vin, est constitué d’une unique couche de polyéthylène, explique Dominique Gessat. Il est évidemment exempt de molécules susceptibles de migrer dans le vin, comme le bisphénol A ou les phtalates. ” Pour le film externe, ce sont au minimum cinq couches qui sont empilées : deux de polyéthylène (PE) à l’extérieur, qui enferment (via une couche de liant permettant le collage) un feuillet d’EVOH, poétiquement baptisé copolymère éthylène-alcool vinylique. C’est le plastique-clé de l’outre du BIB, qui garantit son étanchéité aux gaz et sa résistance mécanique. Il remplace avantageusement les anciens films de polyester métallisé, dans la mesure où sa fabrication se fait par extrusion et non par lamination, ce qui garantit une barrière à l’oxygène plus homogène. L’abandon du polyester métallisé permet en outre de contrôler plus simplement le volume d’air piégé lors du remplissage.
Pas de succès sans R&D
Le travail de la R&D, indispensable pour maintenir la qualité et garantir la sécurité alimentaire, se fait principalement en amont, dans la formulation des plastiques utilisés. En aval, un laboratoire teste, contrôle… et maltraite les matériaux. Pour un film plastique, le laboratoire de Smurfit Kappa doit ressembler à l’antichambre de l’enfer, où ses congénères sont gonflés jusqu’à explosion, torsadés à 440° pendant plusieurs minutes, ébouillantés et percutés par des poids lâchés de plus d’un mètre de haut. L’étanchéité des soudures entre l’outre et le goulot est également contrôlée, ainsi que les niveaux d’oxygène dissous dans le vin. La partie chimique des tests est, quant à elle, confiée à plusieurs laboratoires spécialisés, qui assurent notamment les tests de migration de molécules du plastique vers le vin. Regarderez-vous toujours votre BIB du même œil ?