Sécher du foin tout en produisant de l’électricité
Au Gaec de la ferme du petit Nice, les Limousines se délectent d’un foin exceptionnel grâce à un séchage en grange. Sa mise en place tant technique qu’économique a été rendue possible par la présence de panneaux photovoltaïques.
Au Gaec de la ferme du petit Nice, les Limousines se délectent d’un foin exceptionnel grâce à un séchage en grange. Sa mise en place tant technique qu’économique a été rendue possible par la présence de panneaux photovoltaïques.
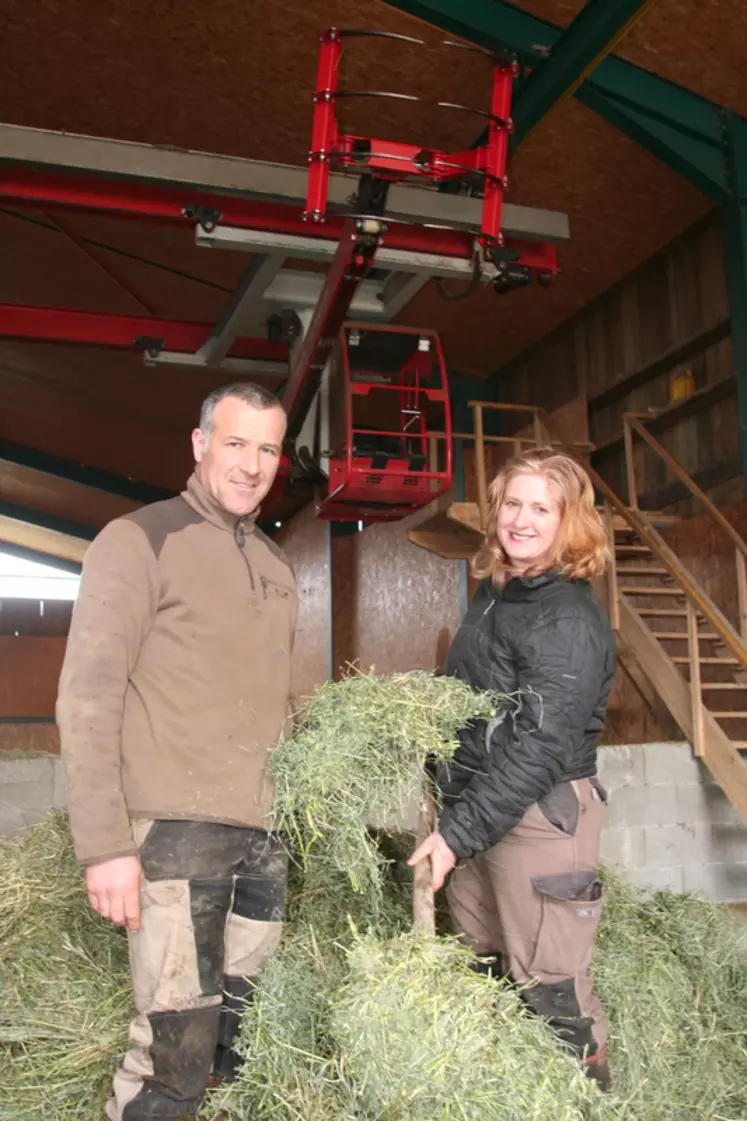

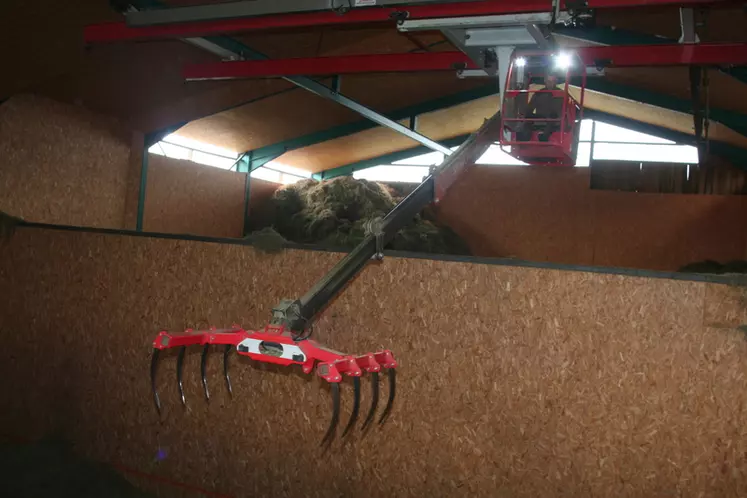
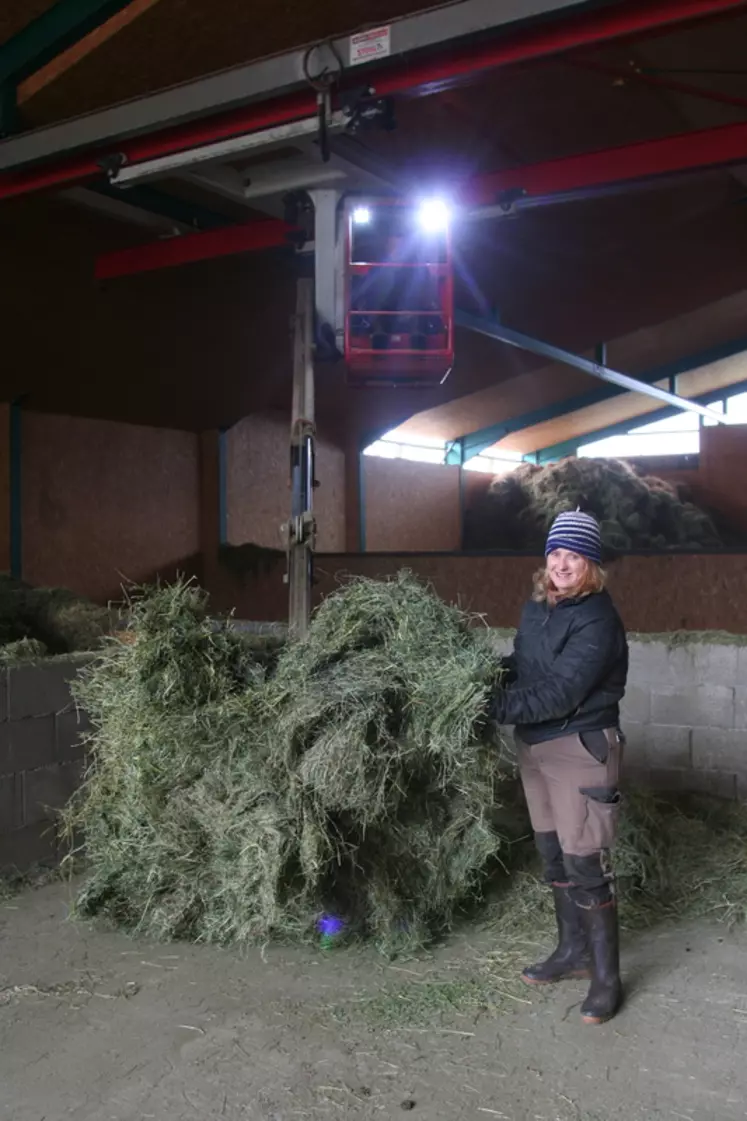
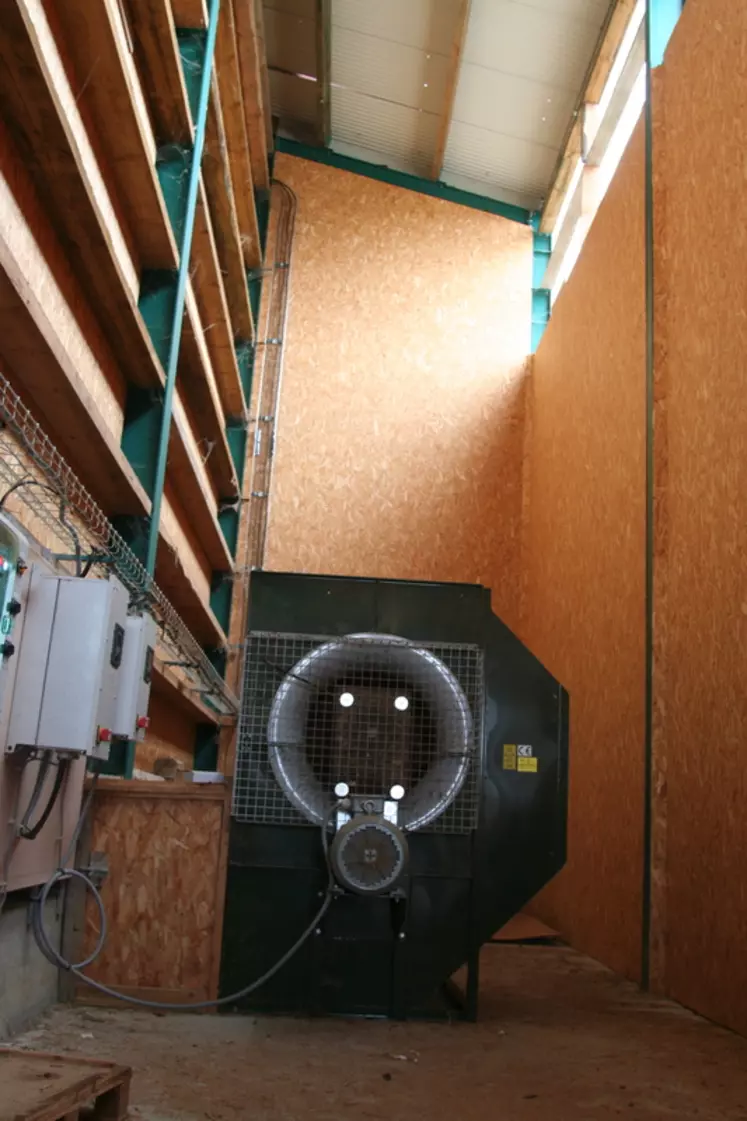

Peut-on trouver un foin plus appétent et de meilleure valeur alimentaire que celui produit chez Denise et Lionel Souvignet ? Oui, peut-être, mais celui produit l’an dernier sur cette exploitation de Haute-Loire est indiscutablement un grand cru. À la fois odorant, très vert, avec encore la quasi-totalité des feuilles sur les tiges de trèfle et de luzerne, il est en un mot superbe. Il est d’ailleurs très apprécié des 70 mères limousines de cette exploitation très orientée sur la vente directe située à mi-chemin entre Le Puy-en-Velay et Saint-Étienne.
Le secret de ce foin cinq étoiles réside dans le séchage en grange mis en service en 2015. Le principal bâtiment de stockage permet simultanément de produire de l’électricité grâce aux panneaux photovoltaïques tout en séchant du foin en vrac grâce à l’air pulsé par des ventilateurs dans le stock de foin. L’air a d’abord été chauffé et asséché en passant entre les panneaux photovoltaïques et un faux plafond en bois.
Chez Denise et Lionel Souvignet, une des deux principales motivations pour envisager cet investissement résidait dans la volonté d’être plus autonome pour l’alimentation du troupeau, en particulier sur le volet protéines. L’exploitation produisait déjà l’essentiel des céréales nécessaires à la finition des bovins de l’exploitation. À côté de cette volonté de faire des économies sur le concentré est venue s’ajouter la nécessité de trouver une solution pour les chantiers d’ensilage d’herbe. Le nombre d’exploitations ayant recours à cette pratique avait diminué sur le secteur et organiser des chantiers dans de bonnes conditions devenait compliqué.
Volonté d’améliorer l’autonomie alimentaire
Sur l’exploitation, les premiers panneaux photovoltaïques avaient été installés dès 2009. C’est dans les années qui ont suivi que les réflexions sur la possibilité d’associer cette couverture des bâtiments à du séchage en grange ont émergé. « On a profité de la vague du développement du photovoltaïque en 2012 pour concrétiser cette idée », explique Lionel Souvignet. La volonté de profiter des tarifs alors très attractifs pour le rachat de l’électricité photovoltaïque a accéléré le mouvement. Deux projets ont été conduits de front : continuer à couvrir le plus possible de toitures avec des panneaux photovoltaïques, tout en travaillant simultanément à la construction du bâtiment de séchage en grange. Ce dernier a été construit en 2012 avec une bonne part d’autoconstruction. Son unité de séchage a été utilisée pour la première fois pour la récolte 2015.
Côté financement, c’est l’électricité produite sur les 1 800 m2 de panneaux et contractualisée aux tarifs de 2012 qui a permis de financer l’investissement. « La quantité produite est en phase avec le prévisionnel. C’est sa vente qui permet de rembourser l’emprunt pour le bâtiment et l’installation de séchage mais également celui réalisé pour couvrir le plus possible de toitures avec des panneaux », souligne Lionel Souvignet. Et d’ajouter « C’est quand même dommage et surtout pas bien normal qu’il faille recourir à de la vente d’électricité pour couvrir cet investissement. Logiquement c’est la vente de viande qui aurait dû le permettre. C’est loin d’être le cas ! »
À l’époque, le bâtiment de stockage incluant l’installation de séchage s’était traduit par un investissement de 246 000 € avec une part importante d’autoconstruction desquels il convient de déduire 42 800 d’aide PPE et PMBE. Le bâtiment a été couplé à l’achat d’une autochargeuse (36 000 €) pour ramener le fourrage depuis les prairies jusqu’au bâtiment. « Sans la vente d’électricité, il est bien certain que nous n’aurions pas pu concrétiser notre projet. »
Climat favorable
Située à 850 m d’altitude, l’exploitation est dans une zone géographique réputée pour la production de salaisons. C’est pour partie lié à la faible hygrométrie de l’air. Cet atout pour faire sécher jambons et saucisses l’est également pour faire sécher l’herbe. « Plus que la température de l’air c’est sa faible hygrométrie qui aide à déshydrater le fourrage. » La météo des trois printemps qui ont suivi la mise en service du bâtiment a été contrastée. « Cela m’a permis de tester différents scénarios. L’an dernier j’ai fait une première coupe le 10 mai et trois jours plus tard, juste après l’avoir rentré, on avait 40 cm de neige ! J’ai réussi à faire sécher le fourrage mais j’étais passablement inquiet. Les fauches précoces sont cependant incontournables dans notre système d’exploitation. On est un peu chargé. Nous avons besoin de parcelles récoltées de bonne heure pour les faire pâturer quelques semaines plus tard. »
Le séchage en bâtiment est indifféremment réalisé avec des premières, secondes ou troisièmes coupes mais il n’est possible de faire sécher que l’équivalent de 10 ha par séance de séchage. On récolte donc moins de surface d’un seul coup comparativement à des éleveurs qui ensilent ou fauchent dans une fenêtre de durée réduite, mais il est possible de mieux choisir la fauche de chacune des parcelles selon l’avancement de la végétation.
« Idéalement en période de beau temps, je fauche dans la matinée. En fin d’après-midi, je vais pirouetter. Le lendemain le fourrage est andainé en fin de matinée et je ramasse le soir ou le lendemain matin selon mon emploi du temps et ce qui est annoncé côté météo. L’idéal c’est de rentrer du fourrage à 60 % de MS. J’ai déjà récolté plus humide (jusqu’à 45 % de MS) quand la météo menace, mais ce n’est pas à préconiser. »
La consommation d’électricité pour faire tourner les ventilateurs est forcément conséquente. Cela équivaut en dépenses au gasoil et aux différentes bâches et filets qui seraient nécessaires si l’herbe était pour partie ensilée et pour partie fanée de façon traditionnelle.
Un tracteur et un télescopique
Il n’y a qu’un tracteur sur l’exploitation et un télescopique. Au moment de la distribution, le foin est repris avec la griffe, posé sur le quai de déchargement puis repris avec le godet du télescopique avant d’être posé dans le couloir des deux stabulations. « Quand on a l’habitude c’est vite fait. » Une grande partie des animaux sont dans une stabulation caillebotis + logettes ou caillebotis + aire paillée avec paille épandue depuis un plafond situé au-dessus des caillebotis, donc pas besoin de pailleuse. Le seul moteur thermique démarré est donc celui du télescopique. « Si on fait la comparaison avec de l’ensilage, je dirai que l’herbe ensilée est plus simple et plus rapide à récolter mais plus complexe à distribuer. » Le foin séché en grange c’est l’inverse. « Côté distribution, le répartir dans les auges est une tâche plaisante et guère fatigante, avec une odeur infiniment plus agréable que celle de l’ensilage », souligne Denise Souvignet. « Hormis la partie engraissement, on a peu de seaux de céréales à distribuer puisque le foin est très riche. C’est aussi plus souple pour la gestion du stock. On n’a pas à se préoccuper de la vitesse d’avancement du silo. Et puis il y a zéro refus. Les vaches s’en rendraient mêmes malades si on les laissait à volonté. Avec de nombreuses parcelles jouxtant des forêts, on retrouve fréquemment des branches dans les auges. On retrouve aussi parfois des fils barbelés ou des cannettes et boîtes de conserve ! Autant de métal qui n’est pas déchiqueté dans l’ensileuse. Sans être une garantie à 100 % notre foin va donc dans le sens d’une réduction du nombre de corps étrangers. »
Satisfaits de leur investissement, Denise et Lionel Souvignet regrettent de ne pas avoir eu la possibilité d’aligner leur bâtiment de séchage avec leur principale stabulation. « Cela nous aurait permis de distribuer le fourrage avec la griffe, sans avoir à le reprendre avec le télescopique. Mais ce n’était pas possible compte tenu de la disposition initiale des bâtiments, du relief et de l’orientation plein sud souhaitable pour le bâtiment de séchage."
Forte proportion de vente directe
L’exploitation fait partie depuis 1999 des pionniers de la vente directe en Haute-Loire. « On finit tous nos animaux et on vend environ 60 % d’entre eux en direct », précise Denise Souvignet, plus spécialement en charge de cette activité tandis que Lionel se concentre sur la conduite du troupeau.
La plupart des mâles sont finis en « veaux rosés légers » abattus autour de cinq mois. Le séchage associé à la production d’électricité est un « plus » lorsque sont organisées des visites à la ferme. Cela contribue à donner une bonne image de l’élevage.
Luzerne et mélanges suisses
Une bonne trentaine d’hectares sont occupés par des prairies temporaires à base de luzerne. « Mais j’ai des difficultés à la maintenir dans ces mélanges car les variétés incorporées dans les mélanges suisses que j’ai utilisés sont trop peu pérennes. » Lionel Souvignet ne craint pas d’avoir un peu de tiges. « Avec notre système de récolte, conserver de la feuille sur la luzerne n’est pas un problème et avoir de la tige favorise la rumination. J’ai des difficultés à maintenir la luzerne quand elle est semée en fin d’été. Surtout avec ces années sèches à répétition où les plantules peinent à être bien en place avant les premiers froids de l’hiver. Je vais tenter cette année du semis direct (40 kg/ha) dans un RGI semé l’automne dernier une fois que j’aurai récolté la première coupe. Je vais aussi tenter un « mélange suisse maison » avec du RGA, de la fétuque, du dactyle et du trèfle blanc avec une luzerne Europe à grosse tige. »
L’installation
L’air sec et chaud situé entre les panneaux photovoltaïques et le plafond en bois est aspiré par les ventilateurs et propulsé sous le tas de foin. Lequel repose sur des caillebotis en bois. L’installation a été dimensionnée pour stocker jusqu’à 900 t de MS mais dans les faits, les tonnages récoltés sont plus proches de 700 TMS répartis en trois cellules de 6 m de haut dont une grande (16x16m) et deux plus petites (16 x 10 m et 15 x 10 m). Un logiciel pilote la ventilation du foin en cours de séchage selon l’hygrométrie de l’air. La température de l’air ventilé gagne à être supérieure d’au moins 5 à 6° à l’air extérieur. Mais c’est davantage son hygrométrie qui est importante. « Il faudrait idéalement 3 m2 de toit pour 1 m2 de surface séchage. Ici on est à 2,5, mais notre bâtiment orienté plein sud compense pour partie cette lacune », explique Lionel Souvignet.