Autoconstruction, mode d’emploi
Ajuster son matériel à son itinéraire technique, économiser du temps, être autonome pour entretenir et réparer ses machines, inventer des outils innovants… Les raisons d’autoconstruire son matériel agricole sont nombreuses. La démarche exige cependant de garantir un bon niveau de sécurité aux utilisateurs.
Ajuster son matériel à son itinéraire technique, économiser du temps, être autonome pour entretenir et réparer ses machines, inventer des outils innovants… Les raisons d’autoconstruire son matériel agricole sont nombreuses. La démarche exige cependant de garantir un bon niveau de sécurité aux utilisateurs.
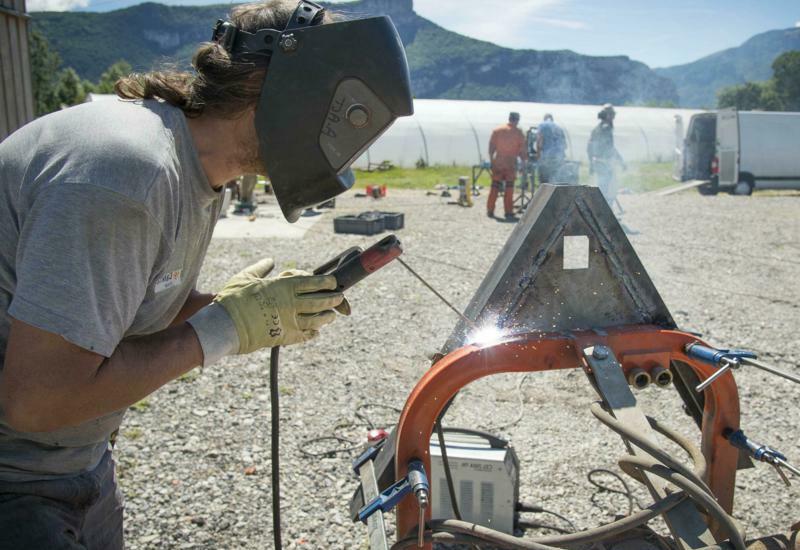



Construire soi-même son matériel agricole, c’est avant tout se doter de machines et d’outils les plus adaptés possibles aux besoins de l’exploitation. C’est en partant du constat que le matériel disponible dans le commerce n’est pas toujours adapté à ces besoins que certains agriculteurs fabriquent ou modifient leurs machines et outils. « Les agriculteurs sont très bien placés pour modifier leur matériel de production, déclare Julien Reynier, chargé de développement à l’Atelier paysan. Chaque ferme a un contexte et des besoins particuliers. Il y a aussi un aspect économique : un matériel autoconstruit peut coûter deux à trois fois moins cher que son équivalent dans le commerce, même s’il faut bien sûr tenir compte du temps passé à la construction ». L’Atelier paysan, créé en 2009 dans l’Isère sous le nom ADABio Autoconstruction par un agronome et un maraîcher, est spécialisé dans la diffusion des savoirs et savoir-faire pour aider les producteurs à être plus autonomes dans la fabrication ou l’entretien de leur matériel. Le réseau, au statut de Société coopérative d’intérêt collectif (SCIC), s’est depuis développé et possède une antenne dans le Finistère en plus de son siège en Isère. « Nous effectuons des tournées de recensement chez les producteurs pour répertorier les innovations, puis nous réalisons des fiches outils disponibles librement sur notre site Internet(1)», détaille Julien Reynier. Avec des groupes d’agriculteurs, l’équipe de l’Atelier paysan développe majoritairement des outils manuels ou des outils à atteler à un tracteur, comme le cultibutte (formation et entretien des buttes) ou la vibroplanche (préparation du sol avant semis ou plantation). Le réseau organise également des stages d’autoconstruction dans toute la France. Ils ont accueilli environ 800 participants en cinq ans.
« Essaimer les connaissances et savoir-faire paysans »
L’Atelier paysan a ses racines dans le maraîchage, et une grande majorité de ces producteurs constructeurs sont eux-mêmes maraîchers, mais la démarche d’autoconstruction s’étend aujourd’hui aux autres filières, arboriculture, viticulture et grandes cultures. Les plans d’un « outil sandwich », développé en partenariat avec le Groupe de recherche en agriculture biologique (Grab) pour réaliser des bandes sandwiches en vergers, sont ainsi disponibles sur le site Internet de l’Atelier paysan. Les producteurs constructeurs peuvent aussi acheter à la SCIC des pièces agricoles ou du petit matériel accessoire, mais pas les outils déjà construits. « Nous n’avons pas vocation à fabriquer ni à vendre des machines agricoles, prévient Julien Reynier. Notre modèle est en revanche le plus adéquat pour essaimer les connaissances et savoir-faire paysans ».
Pour Laurent Lajus, dirigeant de la société de matériel agricole Solhead et vice-président du cluster Machinisme, l’autoconstruction ne doit pas être vue comme une concurrence aux machines du commerce. « C’est une démarche qui a toujours existé et qui existera toujours, annonce-t-il. Mais les agriculteurs qui construisent eux-mêmes doivent, comme tout constructeur, être très vigilants à l’aspect sécuritaire de leurs modifications, surtout si d’autres personnes utilisent le matériel autoconstruit. Il n’y a aucune interdiction à modifier une machine agricole mais, en cas d’accident dû à cette modification, la responsabilité revient à la personne qui l’a faite ». Entre l’autoconstruction et l’achat dans le commerce, une solution intermédiaire consiste à faire appel à un constructeur pour fabriquer un matériel adapté à ses besoins spécifiques (voir l’avis de producteur).
Prendre en compte l’aspect sécurité pour prévenir les risques
Dans tous les cas, les machines agricoles doivent répondre aux exigences essentielles de sécurité. Lorsqu’une machine est achetée dans le commerce, le fabricant fait les démarches pour obtenir le marquage de conformité CE, signifiant qu’elle est conforme aux règles de la directive européenne relative à la sécurité des machines.
« L’autoconstruction a toujours existé et existera toujours »
LAURENT LAJUS, vice-président du cluster Machinisme
En revanche, si la machine est autoconstruite ou modifiée par un agriculteur, c’est à lui de faire cette démarche. L’autocertification est une procédure simplifiée permettant d’obtenir le marquage CE (voir encadré). « La certification ne dédouane pas le constructeur ou l’autoconstructeur de sa responsabilité en cas d’accident, mais c’est un signe que l’aspect sécurité a été pris en compte lors de la fabrication », explique Laurent Lajus. Comme les constructeurs, les autoconstructeurs ne sont jamais complètement à l’abri d’avoir des ennuis en cas d’accident. Mais toutes les précautions sont bonnes à prendre pour, d’une part, assurer la sécurité des utilisateurs, et d’autre part, se protéger juridiquement. D’abord lors de la conception : choisir des matériaux adaptés, vérifier chaque soudure, éviter l’ajout de pièces dangereuses… sont autant de mesures indispensables à prendre lorsque l’on modifie une machine. Une fois la machine construite, former les utilisateurs à son usage et avertir des risques par une notice d’utilisation sont des bonnes manières de prévenir les accidents. « Si la machine autoconstruite présente des risques d’accident, je recommande de faire valider l’aspect sécuritaire par un organisme vérificateur, conseille Laurent Lajus. Cela a un coût, de 300 à 3 000 euros selon la complexité de la machine, mais cela permet de diminuer encore les risques ». Enfin, les réglementations européennes en matière de sécurité des matériels ne sont pas immuables. Idéalement, un producteur qui pratique l’autoconstruction doit se tenir au courant des évolutions réglementaires...
Une machine est, selon la directive européenne 2006/42/CE, un équipement pourvu d’un système d’entraînement autre que la force humaine ou animale, autrement dit un équipement motorisé.
Les outils, qui désignent les équipements agricoles non motorisés, mus par la force humaine ou animale, ne sont eux pas soumis au marquage CE et donc à l’autocertification.
Les trois étapes de l’autocertification
-
1. Établir un dossier technique
Le dossier technique permet de vérifier que la machine est conforme aux exigences essentielles de santé et de sécurité. Il doit être disponible pour toute autorité souhaitant vérifier la validité de la déclaration CE de conformité et doit être conservé dix ans après la date de fabrication.
Il comprend notamment :
une description générale et les plans de la machine,
les plans des circuits de commande,
une documentation sur l’évaluation des risques et les solutions mises en oeuvre pour atteindre un niveau de sécurité conforme aux exigences de la réglementation,
la notice d’instruction de la machine : renseignements généraux sur la machine (désignation, fonction, poids, puissance, niveau de bruit…), instructions sur le montage et la mise en service, l’utilisation, les équipements de protection nécessaires, la maintenance, les réglages…
-
2. Rédiger et signer la déclaration CE de conformité
Ce document atteste que la machine respecte les règles de sécurité décrites dans les directives et normes qui la concernent.
-
3. Apposer le marquage CE sur la machine
Chaque machine doit porter, de manière lisible et indélébile, un marquage comprenant les indications suivantes : la raison sociale et l’adresse complète du fabricant, la désignation de la machine, l’année de construction et le marquage CE.
A trouver sur le site www.entreprises.gouv.fr/libre-circulation-marchandises/marquage-CE
-
J’ai fait construire une machine adaptée à mes propres besoins
« Il y a une dizaine d’années, je cherchais à améliorer mon chantier de récolte de choux-fleurs. Mon objectif était d’améliorer le confort, de limiter le nombre de manipulations, et surtout de pouvoir travailler seul sur le chantier de récolte. Je suis entré en contact avec un fabricant, Jean-Yves Jacq, pour lui acheter un automoteur d’occasion, mais il m’a informé qu’il ne correspondait pas à mes besoins. Cependant, mon idée l’intéressait et il m’a proposé de travailler à deux pour concevoir un débardeur automoteur pour la récolte. Nous nous sommes rencontrés une quarantaine de fois en un an pour la conception de la machine et l’élaboration du cahier des charges. Lui envisageait plus l’aspect construction et moi l’aspect utilisation. Au bout d’un an, nous avons abouti à un prototype qui convenait. Je n’aurais pas pu construire ce débardeur moi-même car il comporte beaucoup d’éléments hydrauliques. Cette machine parfaitement adaptée à mes besoins m’a permis de beaucoup gagner en confort sur la chantier de récolte, ce qui était l’objectif initial, mais aussi d’être nettement plus productif ! J’en ai depuis acheté un autre, qui présente peu de modifications par rapport au prototype. Le fabricant a également construit plusieurs autres débardeurs, à la demande de producteurs. Chaque exemplaire présentant des spécificités selon les besoins de chacun ».
A monter soi-même
Déjà propriétaire d’un quad, Guillaume Thomas, responsable de l’EARL Anjou Muguet et producteur d’asperge dans le Maine-et-Loire, a choisi l’option « en kit » pour s’équiper d’un pulvérisateur à adapter sur son engin. « J’ai acheté à la carte et selon mes besoins la cuve, la pompe et les supports de buses », explique le professionnel. Seule l’adaptation de la cuve à l’arrière du quad, qui nécessitait l’installation d’un raidisseur d’amortisseur pour supporter la charge de la cuve, a été réalisée par un chaudronnier. Pour le reste, Guillaume Thomas a effectué le montage des éléments selon les contraintes du désherbage des asperges. Ainsi, les « aiguilles » supportant les buses permettent de s’approcher au plus près des adventices sous la végétation déjà développée. L’appareil conçu, en partie par le producteur, permet d’assurer le désherbage de rattrapage dans ses aspergeraies. « Avec peu de temps de construction, qui se composait essentiellement de montage, je dispose d’un matériel adapté à mes besoins avec un investissement assez limité. Le travail de montage facilite désormais la maintenance et parfois la modification du matériel pour d’autres usages comme le désherbage des abords de parcelles », explique le producteur qui utilise régulièrement son matériel sur une quinzaine d’hectares.