Moteur – Pourquoi JCB s’oriente vers l’hydrogène et l’électrique ?
Le constructeur britannique JCB conduit depuis plusieurs années des recherches dans le domaine de la motorisation pour satisfaire à l’objectif de fabriquer des machines zéro émission à l’horizon 2050. Les différentes pistes étudiées l’amènent aujourd’hui à s’orienter vers deux solutions majeures : l’électrique et l’hydrogène.
Le constructeur britannique JCB conduit depuis plusieurs années des recherches dans le domaine de la motorisation pour satisfaire à l’objectif de fabriquer des machines zéro émission à l’horizon 2050. Les différentes pistes étudiées l’amènent aujourd’hui à s’orienter vers deux solutions majeures : l’électrique et l’hydrogène.
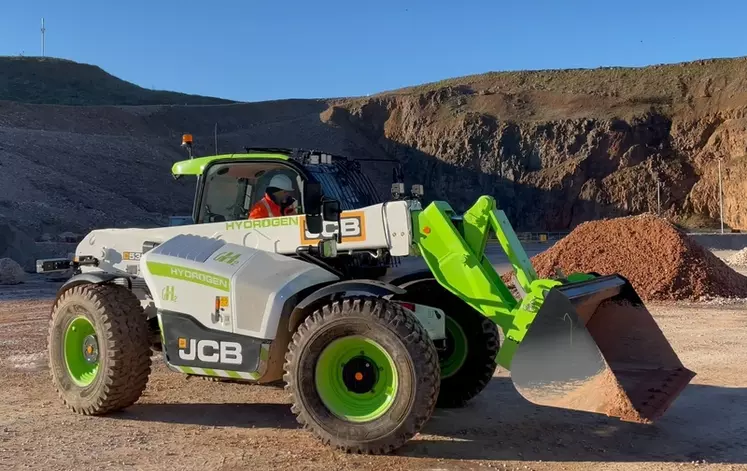
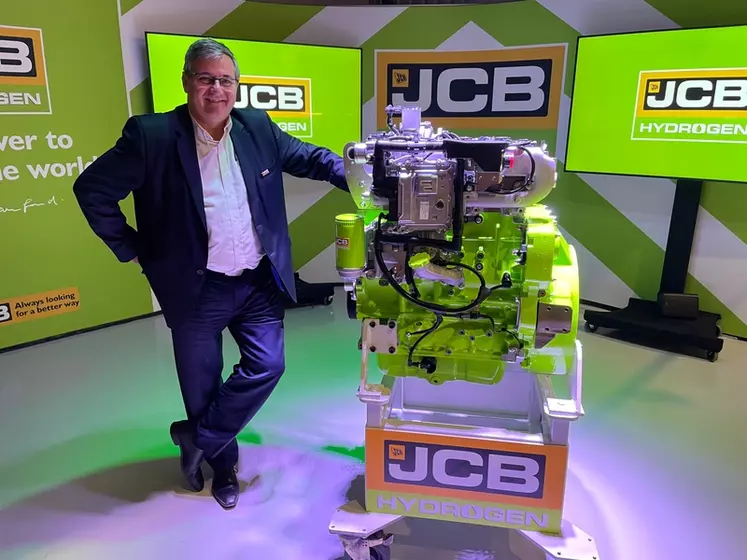
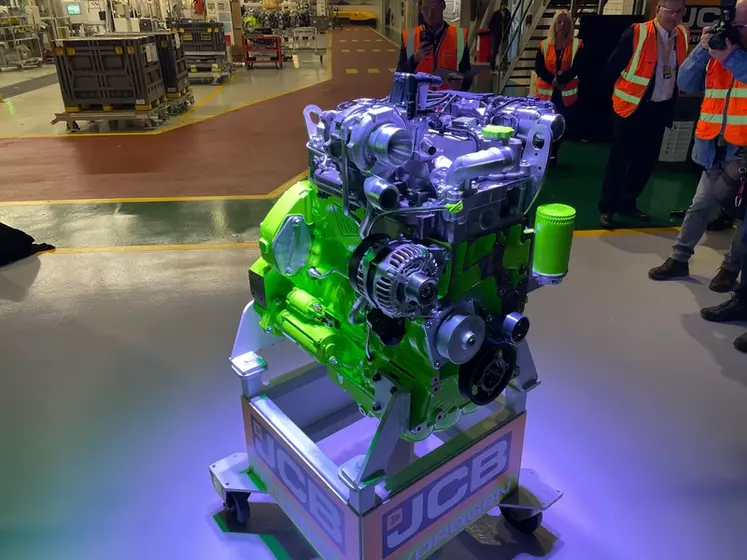
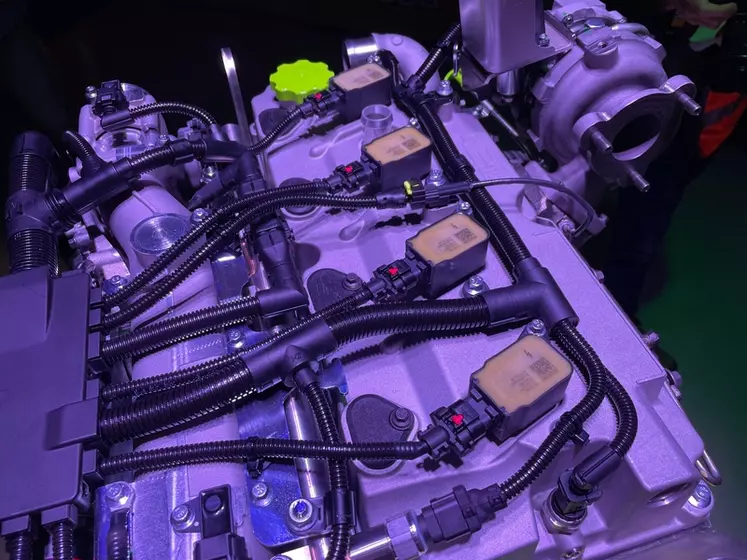
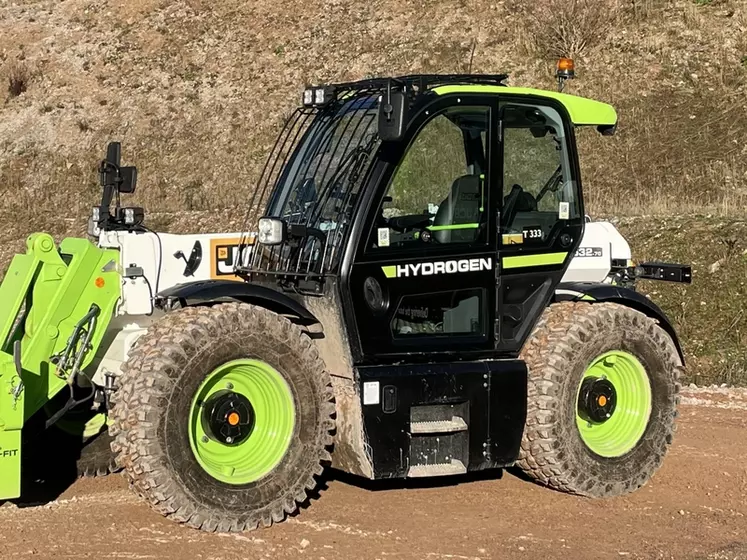
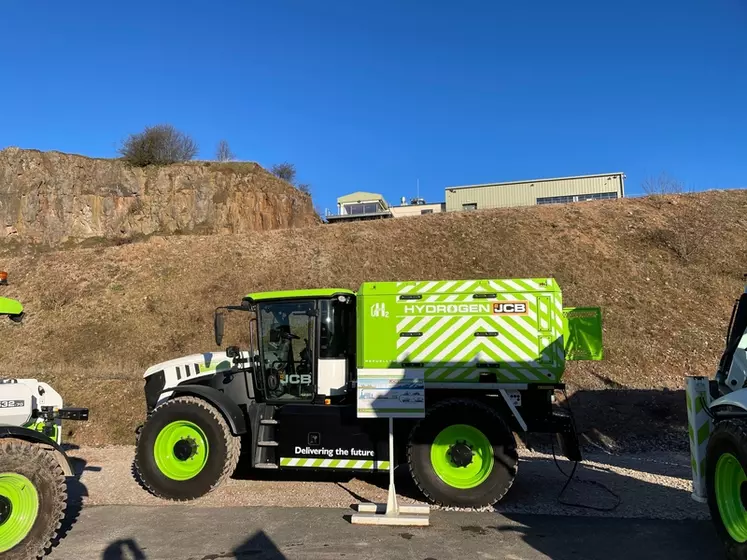
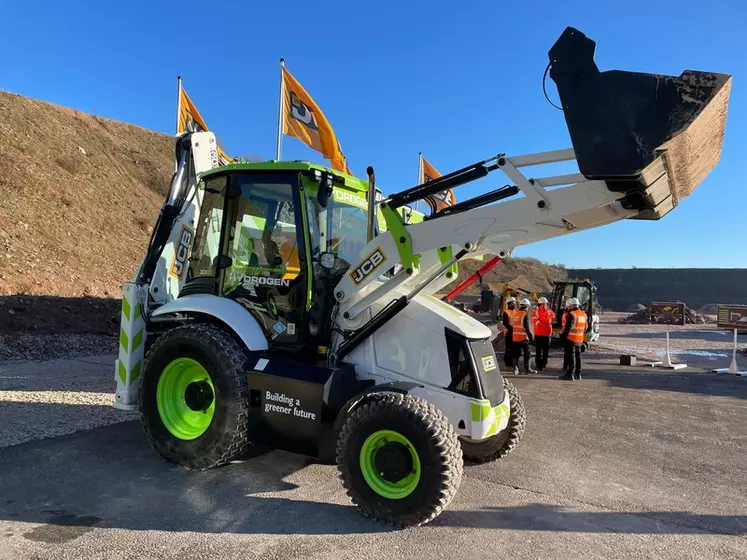
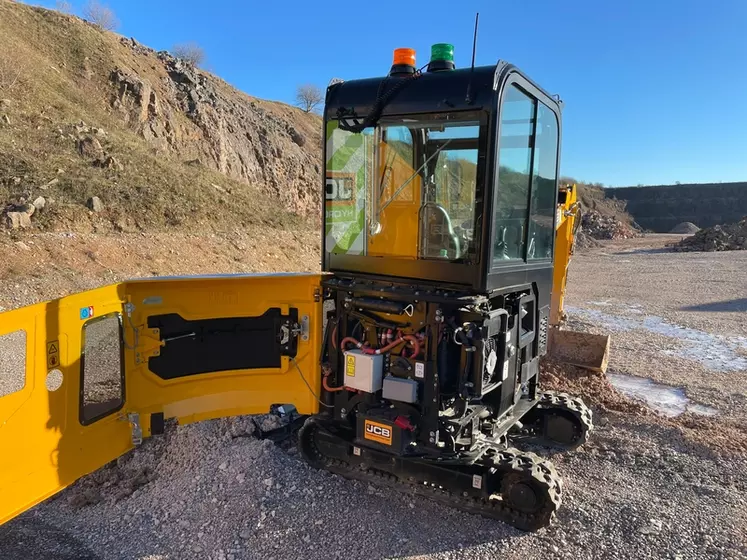
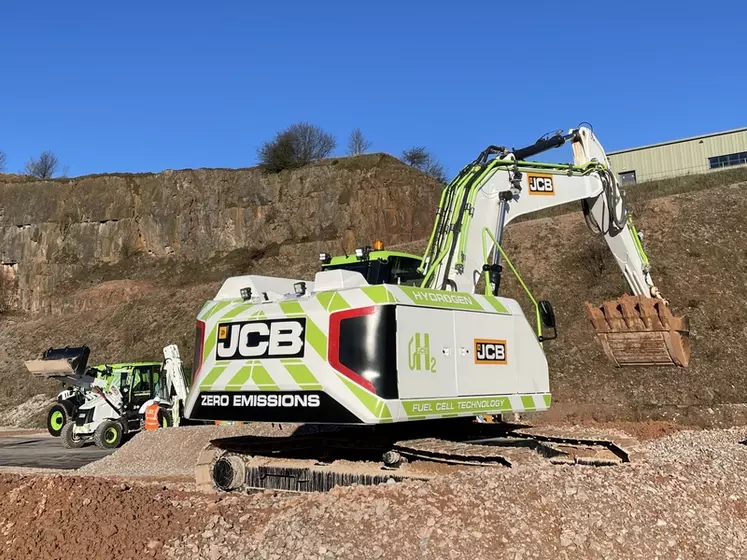
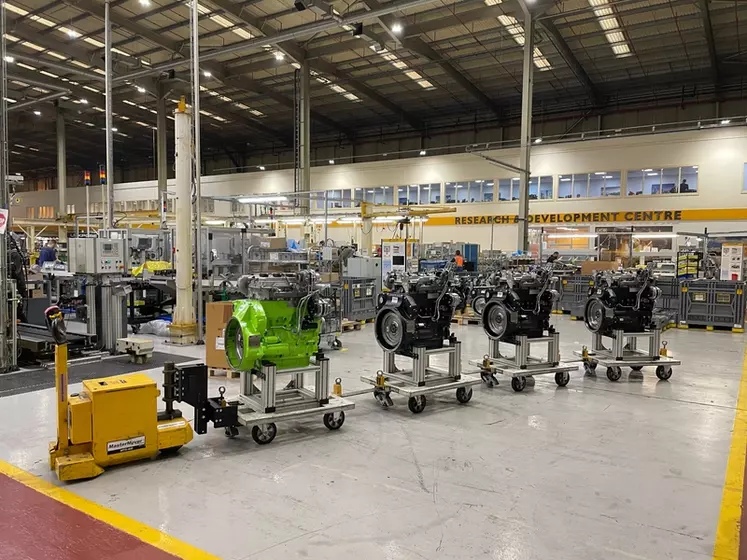
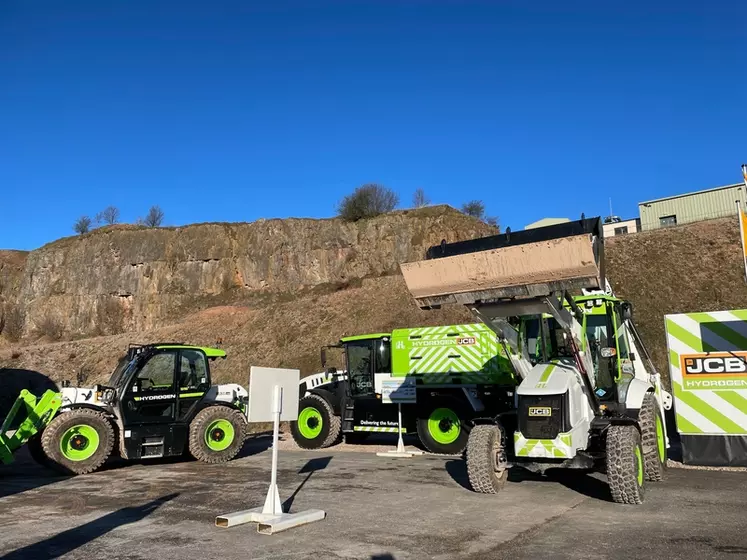
À voir les derniers développements de JCB, le moteur thermique a encore de belles années devant lui. Le constructeur britannique vient en effet de dévoiler une déclinaison fonctionnant à l’hydrogène (H2) de son quatre cylindres JCB 448 de 4,8 l. Découvert en action sur un chargeur télescopique et sur une tractopelle, ce moteur, qui partage sa conception avec les modèles diesel de la marque, adopte un module conçu spécialement pour l’injection de H2, ainsi qu’une culasse et un turbocompresseur spécifiques. L’explosion du mélange air-hydrogène est assurée par une bougie, comme sur un moteur à essence. Sur le plan des performances, la firme britannique annonce des valeurs de couple et de puissance similaires à celles de la version diesel. Le premier modèle développé délivre pour le moment 55 kW (75 ch) et son couple atteint 440 Nm, mais il sera à terme décliné dans des puissances supérieures (jusqu’à 130 kW - 174 ch). JCB prévoit aussi d’intégrer la technologie H2 sur ses autres quatre cylindres de 3 et 4,4 l, ainsi que sur le six cylindres de 7,2 l.
Fini l’EGR, le FAP et l’AdBlue
Le fonctionnement à l’hydrogène ne change rien côté maintenance, car les intervalles d’entretien restent identiques, même si au bout de 500 h l’huile garde sa couleur d’origine, n’étant pas polluée par la combustion d’hydrocarbures. Un des gros avantages induits est la disparition des systèmes antipollution, avec l’abandon de l’EGR, du filtre à particules et de l’AdBlue. Selon les ingénieurs de JCB, les émissions de NOx sont négligeables et ne nécessitent pas de traitement spécifique. Pour l’alimentation du moteur, l’H2 est stocké à une pression de 350 bars dans des bonbonnes renforcées au Kevlar procurant une autonomie d’une journée de travail. Le ravitaillement sur les chantiers s’opère notamment à l’aide d’une station mobile mise au point par JCB. Comme 1 kg d’hydrogène équivaut en termes d’autonomie à 3 litres de GNR, selon JCB, et que son prix est de 6 à 8 euros le kilogramme, le coût d’utilisation s’avère légèrement supérieur, mais il est appelé à baisser avec l’augmentation de la production. L’hydrogène n’est pas la seule solution proposée par JCB pour animer sa large gamme de machines. Pour atteindre l’objectif de zéro émission, il retient en effet la fée électricité pour ses plus petits matériels, à l’instar des dumpers, des nacelles, des minipelles, des chariots élévateurs et des chargeurs télescopiques compacts.
10 tonnes de batteries sur le Fastrac
Le recours à l’entraînement électrique présente l’avantage d’obtenir des machines performantes et silencieuses. Il a l’inconvénient d’augmenter considérablement le prix. À performance et autonomie comparables, une minipelle électrique coûte 1,7 fois plus cher qu’une variante thermique, une différence liée exclusivement au prix de la batterie, car l’architecture de la machine ne change pas. Si cela est acceptable sur des engins compacts, il n’en est pas de même pour les grosses machines, car au tarif s’ajoute le problème d’encombrement des accumulateurs électriques. Par exemple, pour obtenir 16 heures d’autonomie en électricité avec le Fastrac, ce tracteur verrait son prix multiplier par quatre et surtout il devrait embarquer une batterie pesant 10 t (5 t pour 8 h d’autonomie et prix multiplié par 2,7 ; 2,5 t pour 4 h et prix multiplié par 1,9). Se pose par ailleurs la question de la durée de vie des batteries, de leur recyclage et du coût de leur remplacement.
Les limites de la pile à combustible
Avant de s’orienter vers l’hydrogène, JCB a étudié différentes pistes de carburant mobile, comme le biométhane, le HVO et l’ammoniac. Le constructeur travaille aussi sur la pile à combustible (appelée aussi Fuel Cell) et dispose d’une pelle mécanique de 22 tonnes équipées de cette solution. Selon ses observations, cette technologie est compliquée à mettre en œuvre et demande notamment d’embarquer sur la machine un important dispositif de refroidissement. En plus d’être onéreuse, elle présente l’inconvénient d’être fragile et de ne pas accepter l’atmosphère poussiéreuse, ce qui limite son intérêt en agricole et dans le domaine des travaux publics.
Comment produire de l’hydrogène vert ?
L’hydrogène est un gaz inodore et incolore qui se classe pourtant en différentes couleurs selon son mode de production. Les plus courants, le gris et le noir, sont produits à partir d’hydrocarbures et ne sont donc pas les plus vertueux, car ils sont source d’émissions de CO2. Le jaune est fabriqué par électrolyse (séparation électrique des molécules d’hydrogène H2 et d’oxygène O contenues dans l’eau H2O) à partir de l’électricité issue des centrales nucléaires. L’hydrogène vert est considéré comme le plus propre, car il est produit à partir de l’énergie provenant des éoliennes, des centrales photovoltaïques et des unités de méthanisation en cogénération, toutes étant des énergies renouvelables. Ce gaz a l’avantage de pouvoir être produit par tout le monde, à condition de disposer d’une ressource en eau, et ouvre la voie vers l’autonomie énergétique. Il présente également l’intérêt de valoriser, par l’électrolyse de l’eau, l’électricité produite en surplus. La production d’électricité par ces sources d’énergie intermittentes ne coïncide pas toujours avec les pics de consommation et une partie de l’électricité produite est bien souvent perdue.