Grégoire abat les murs pour augmenter sa production de 50 %
Derrière les murs extérieurs du site de Châteaubernard, Grégoire réorganise en profondeur son outil de production, pour le rendre plus flexible et performant.
Derrière les murs extérieurs du site de Châteaubernard, Grégoire réorganise en profondeur son outil de production, pour le rendre plus flexible et performant.
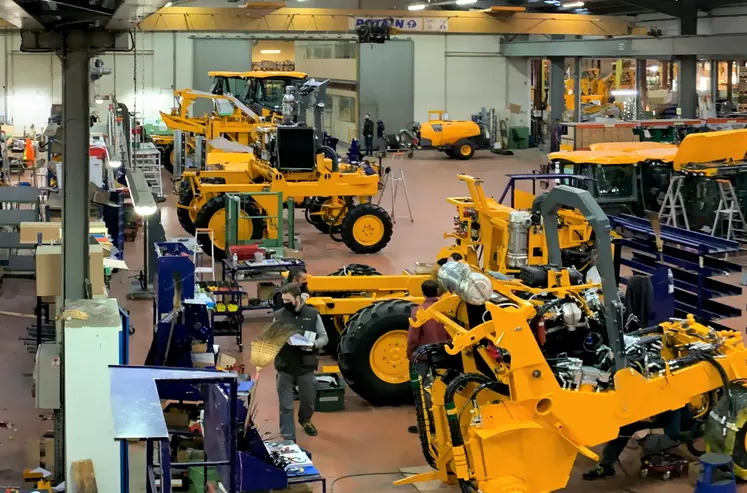
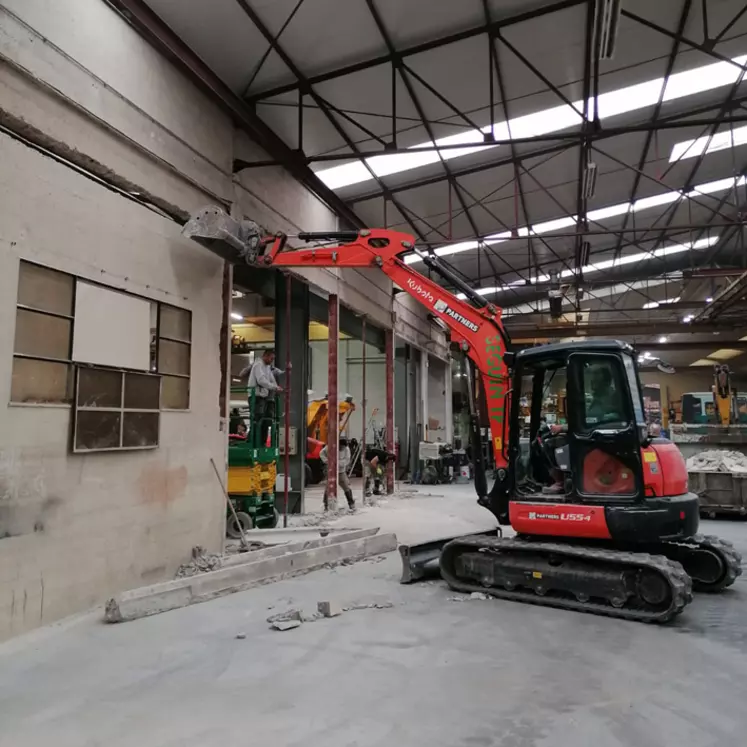

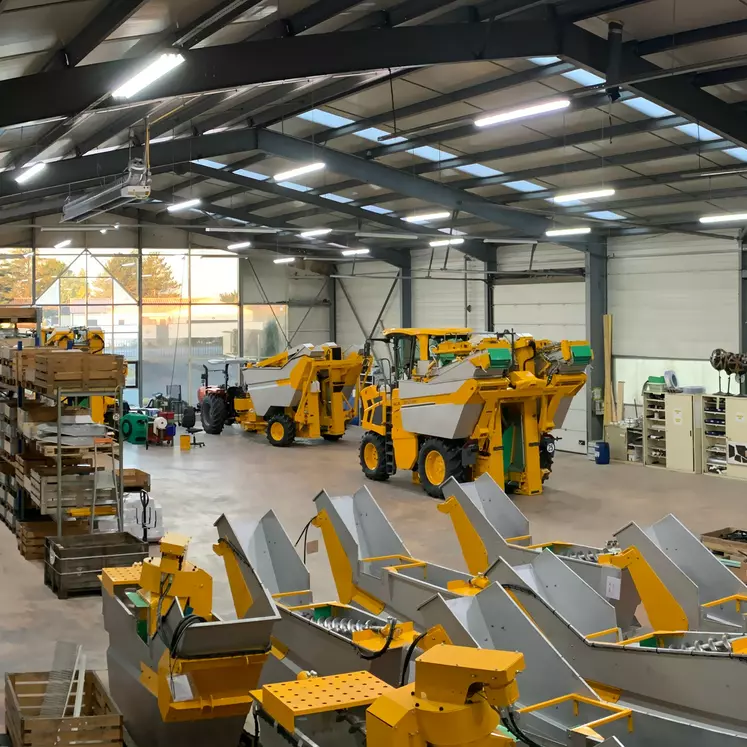
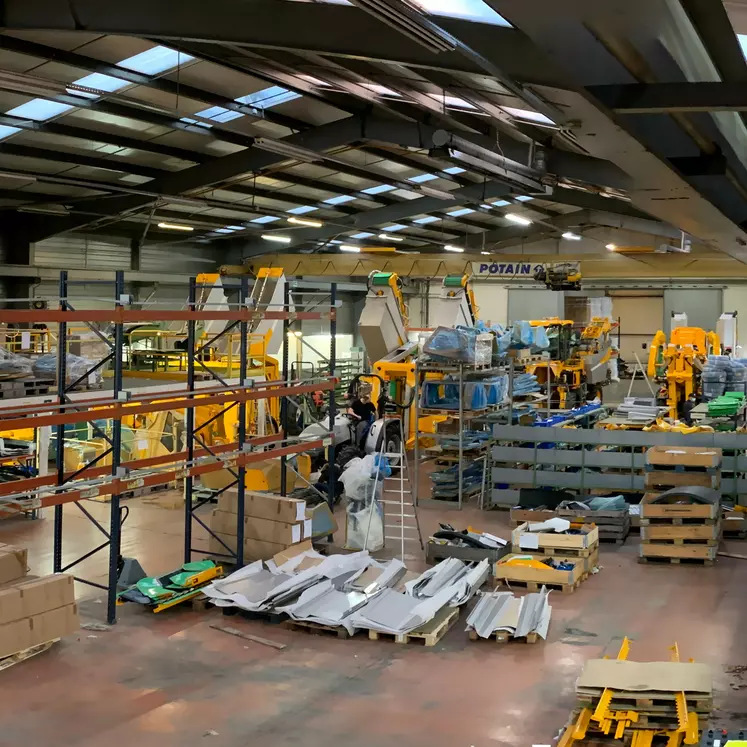
Depuis septembre 2021, le constructeur charentais Grégoire réorganise en profondeur son usine de Châteaubernard, près de Cognac, tout en maintenant la production. "Nous étions arrivé au maximum de notre outil de production, fruit de 50 ans d'histoire et de bâtiments qui se sont greffés les uns aux autres, explique Christophe Baron, responsable communication chez Grégoire. L'un des choix, peut-être le plus simple, aurait été de tout reconstruire ailleurs. Nous avons plutôt fait le choix de rester dans nos murs et d'opérer une transformation profonde tout en continuant à produire nos machines." La première étape a été la réfection des toits, qui ont été désamiantés, rendus beaucoup plus lumineux et isolés : les opérateurs y ont gagné en confort de travail.
Une production à géométrie variable
La seconde étape a été de casser entre les différents bâtiments les murs qui ankylosaient la chaîne de montage : Grégoire a profité de la coupure des fêtes de fin d'année pour mener à bien cette opération, sans trop impacter la production. "L'idée est d'avoir une production à géométrie variable, dont la volumétrie évolue en fonction de la saisonnalité", explique Christophe Baron.
À titre d'exemple, la production des pulvérisateurs a intégré le site principal de Châteaubernard. Cette nouvelle organisation impose également une formation du personnel pour le rendre plus polyvalent : face à une pénurie de main-d’œuvre, un gros effort a été porté sur la formation en alternance.
Un flux en "arête de poisson"
La production suit désormais un flux en "arête de poisson", agencé autour d'une ligne de montage principale. Le nouvel espace de préparation des moteurs et celui de la production des cabines ont ainsi été rapprochés de la ligne de montage des porteurs. Il en sera de même des modules tête de récolte, benne et systèmes de tri embarqués. Le temps de montage de chaque machine va être réduit, améliorant la gestion des stocks et impactant positivement la trésorerie. "Cet argent économisé pourra être investi ailleurs, par exemple en recherche et développement. "
À terme, la capacité de production, jusque-là limitée à 300 machines par an, devrait croître d'au moins 50 %.
L'une des prochaines étapes s'attaquera aux bureaux et aux espaces de réception, notamment le show-room et les locaux de formation.