Le point sur les caissons de nettoyage des moissonneuses-batteuses
L’efficacité du caisson de nettoyage détermine le débit des moissonneuses-batteuses. Son optimisation passe par l’adoption d’automatismes plus ou moins complexes.
L’efficacité du caisson de nettoyage détermine le débit des moissonneuses-batteuses. Son optimisation passe par l’adoption d’automatismes plus ou moins complexes.
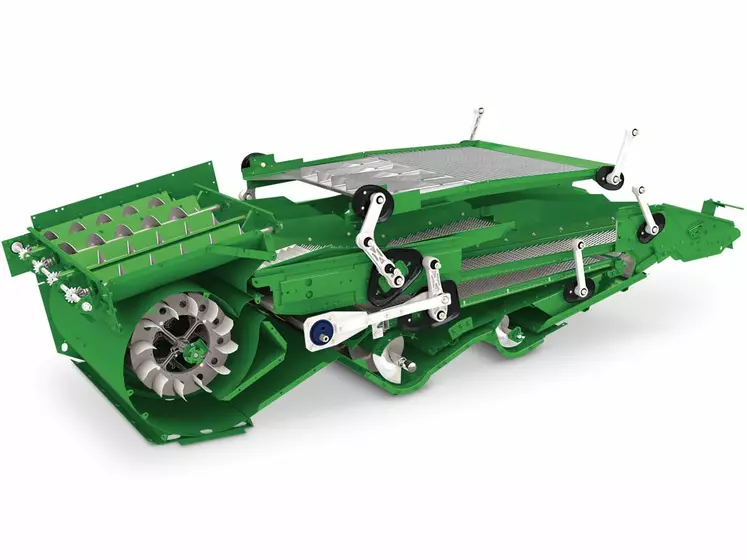
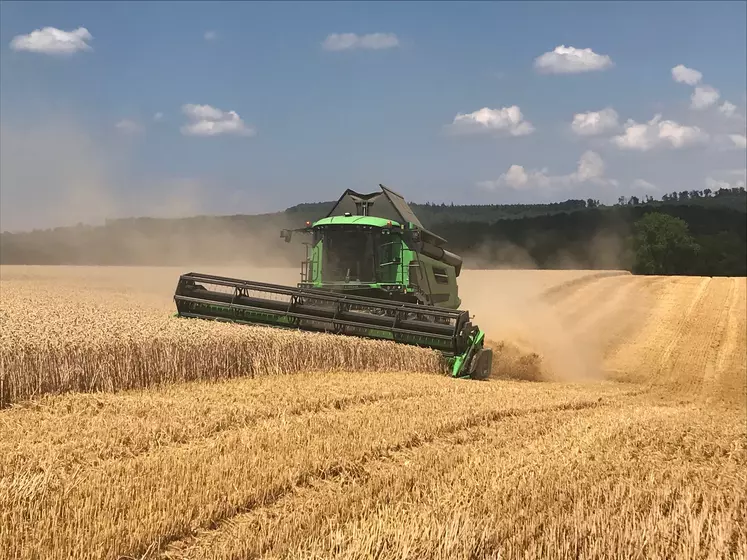
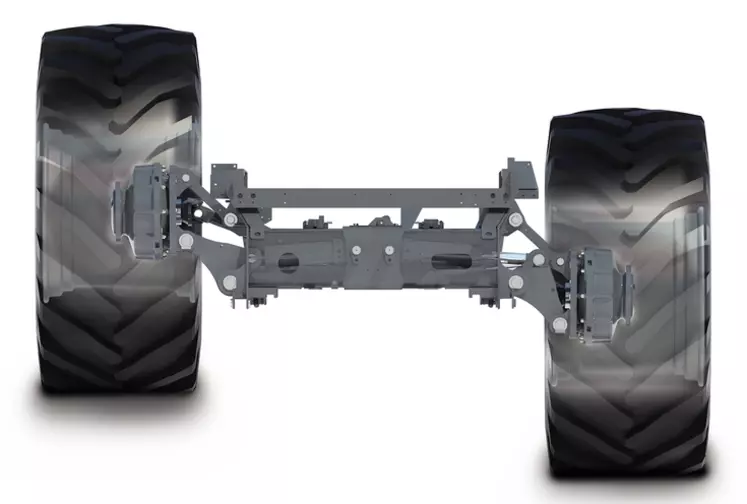
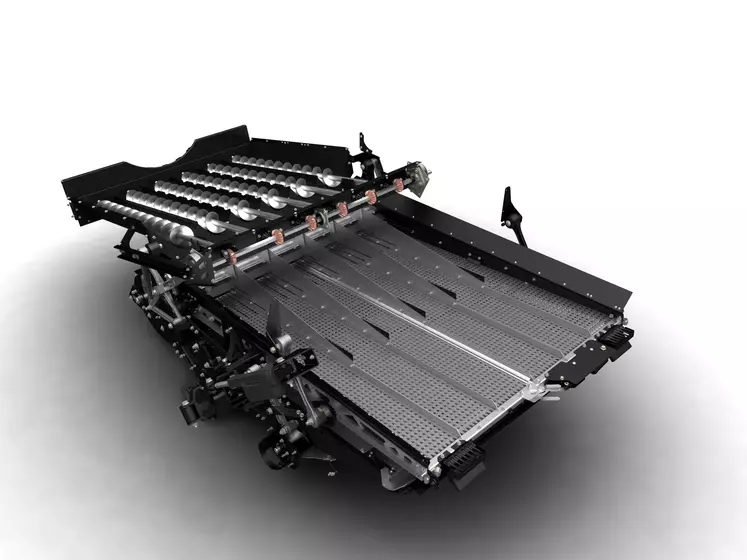
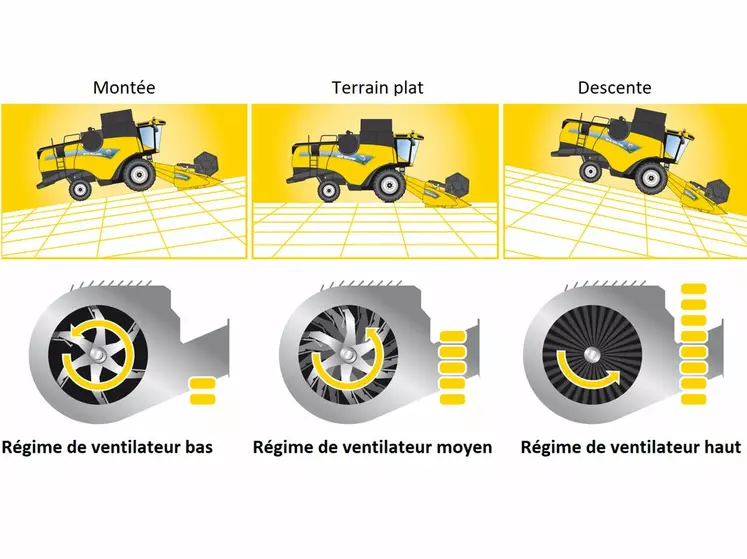
Les caissons de nettoyage voient, à pleine charge, passer jusqu’à 60 tonnes de récolte par heure, voire plus de 100 tonnes sur les moissonneuses-batteuses les plus puissantes. Leur surface, variant de 3,4 à plus de 6 mètres carrés, dépend de la taille des machines, du mode de séparation (battage conventionnel, hybride, simple ou double rotor longitudinal) et de leur architecture à simple, double ou triple chute. Ces cascades formées, par des prégrilles de nettoyage, se situent entre la table de préparation et la grille supérieure. Traversées par la ventilation, elles évacuent une grosse partie des menues-pailles, bales et autres impuretés, évitant de surcharger les grilles. Tous les caissons fonctionnent correctement à plat. Dans cette configuration idéale, les grilles sont recouvertes uniformément par le matelas de récolte, qui peut atteindre 20 cm d’épaisseur, et le flux d’air qui les traverse est alors parfaitement réparti. Ainsi, les menues-pailles sont expulsées par la ventilation vers l’arrière de la machine, les ôtons sont recyclés vers le batteur ou la table de préparation, et seule la récolte propre monte en trémie. Ces conditions idéales ne sont représentatives de toutes les régions françaises. Les moissonneuses-batteuses doivent donc se montrer performantes dans toutes les situations, en s’affranchissant des contraintes imposées par le relief, y compris par les petits dénivelés. « Si les grilles sont davantage remplies d’un côté que de l’autre, le flux d’air provenant de la turbine va au plus facile, le nettoyage est incorrect et la machine perd du grain », prévient Guillaume Feys, coordinateur des chefs produits automoteurs chez Claas. Les constructeurs rivalisent alors d’ingéniosité pour assurer le fonctionnement optimal de leur machine.
La ventilation sous contrôle
Pour garder le caisson à plat, différents procédés mécaniques existent. La solution la plus efficace est de corriger mécaniquement l’assiette de la moissonneuse-batteuse. Les marques montent alors des réducteurs de roue avant articulés, gardant la machine à l’horizontal dans les dévers de 18 à 22 %, selon les marques. Ce principe prend l’appellation Hillmaster chez John Deere, Montana chez Claas, ParaLevel chez Agco (Fendt, Massey Ferguson et Laverda), Balance chez Deutz-Fahr, Latérale ou Everest chez New Holland… Encore plus performants, les lève-arrières, associés à des essieux avant articulés hydrauliquement, équipent des modèles de gabarit moyen, spécialement conçus pour récolter en coteaux. Par exemple, les cinq-secoueurs New Holland TC et CX Hillside restent horizontales en descente jusqu’à 10 %, en montée jusqu’à 30 % et en dévers jusqu’à 38 %. Le caisson autonivelant est aussi une solution pour préserver l’efficacité, tout comme le cloisonnement de la table de préparation et des grilles. Leur capacité de correction s’avère, en revanche, plus limitée. L’optimisation des systèmes de nettoyage pour satisfaire aux débits grandissants des moissonneuses-batteuses passe également par l’utilisation d’automatismes intrinsèques au caisson. Par exemple, l’uniformité du matelas de récolte peut se contrôler en exerçant un mouvement latéral sur les organes de nettoyage ou en dirigeant le flux de produit traversant les organes de battage et de séparation. Le flux d’air doit, aussi, être parfaitement ajusté pour assurer uniquement l’expulsion des menues-pailles et autres impuretés. Plusieurs marques, comme Claas, John Deere et New Holland, adoptent alors la gestion automatique des vents en fonction de l’angle longitudinal de la machine. Avec ce dispositif, le régime de la ventilation est abaissé dans les montées, alors qu’il augmente dans les descentes. Il s’accompagne, sur certains modèles, de la modification de l’ouverture des grilles. Tous ces équipements représentent un investissement supplémentaire méritant une approche précise en fonction des contraintes de récolte, afin de garantir le retour sur investissement.
New Holland mesure la puissance du flux d’air
Les caissons de nettoyage New Holland se distinguent par l’intégration d’une première chute sur une prégrille dirigeant 30 % du volume de récolte directement sur la grille inférieure. Le but de cette architecture est de limiter le chargement de la grille supérieure à ôtons. Les modèles TC, CX5 et CX6 profitent en plus du procédé Smartsieve de correction du dévers jusqu’à 25 %, selon le constructeur. Ce dispositif génère un mouvement latéral de la prégrille et de la grille supérieure, afin de répartir le matelas de produit sur toute leur largeur. Les New Holland CX5 et CX6 bénéficient, elles, d’un caisson à triple chute entre la table de préparation et la grille supérieure. Le fameux caisson autonivelant, bien connu sur les TX, est toujours d’actualité sur les CX7, CX8 et CR. D’appellation Opti-Clean, il prend place dans un châssis spécifique et garde à plat l’ensemble des éléments de nettoyage dans les dévers jusqu’à 17 %. La dernière innovation chez New Holland est le système Intellisense de gestion automatique des réglages de la machine. Ce dispositif, exclusif aux CR, utilise un capteur mesurant la pression au-dessus et en dessous de la grille supérieure. En fonction des données relevées avec une précision de 0,01 millibar, l’électronique agit sur le régime des vents ou sur l’ouverture des grilles.
Un caisson unique chez John Deere
John Deere a fait le choix, en 2016, d’uniformiser le caisson de nettoyage sur les moissonneuses-batteuses des séries W, T et S. La solution à triple chute Dynaflo+, appliquée en 2017 sur les S, se caractérise par son montage riveté plutôt que soudé pour davantage de robustesse, l’utilisation de longerons en aluminium afin de réduire les contraintes et l’inertie des pièces en mouvement, ainsi que par la longueur des grilles (presque 2 mètres pour la supérieure). Ventilé par une turbine à 12 pales, le caisson profite d’une prégrille nettoyant 40 % du grain avant sa chute sur la grille supérieure, afin de ne pas la surcharger. Son alimentation est assurée par une table de convoyage composée de vis sans fin, qui collectent le produit provenant des organes de battage et de séparation. Pour la compensation des dévers, le constructeur américain annonce une correction jusqu’à 7 % grâce aux cloisons longitudinales de 10 cm de haut placées en standard sur les organes de nettoyage (table, prégrille, grilles…). Un kit composé de compartiments d’environ 20 cm de haut et de volets en polymère repousse la compensation à 14 %. Les déflecteurs souples, placés sur le flanc des cloisons et répartis sur toute leur longueur, balayent le flux de récolte et le répartissent sur la largeur du compartiment. Les machines des séries S accèdent en exclusivité à l’automatisme ATA (Active Terrain Adjustment) modifiant, en montée et en descente, la vitesse des vents et l’ouverture des grilles à ôtons et à grains. Pour 2019, les machines des séries W et T profitent d’améliorations sur la table à triple chute pour un meilleur effet autonettoyant. Les modèles à six secoueurs voient aussi le nombre de vis convoyeuses passer de 7 à 6 pour une distribution plus uniforme de la matière.
Deutz-Fahr recycle les ôtons sur la table de préparation
Le caisson des nouvelles moissonneuses-batteuses Deutz-Fahr de la série C9300 disposent d’une double chute en bout de table de préparation. Cette cascade élimine les plus grosses impuretés et nettoie un tiers du grain, selon le constructeur. Le flux d’air est fourni par une turbine à 44 pales garantissant une ventilation homogène sur toute la largeur. Le système de recyclage des ôtons reste, lui, conformes aux habitudes de la marque. Il utilise deux mini-batteurs, un de chaque côté, qui renvoient les grains et les bales sur la table de préparation.
Compensation de dévers 4D pour Claas
Le caisson de nettoyage à double chute Jet Stream de Claas adopte le système de compensation 3D maintenant les performances dans les dévers jusqu’à 20 %. Ce procédé actionne latéralement la grille supérieure pour uniformiser le matelas de récolte. La dernière évolution apportée sur le caisson est l’adoption de la compensation de dévers 4D sur les Lexion 700. En pratique, le dispositif de battage et de séparation de ces machines à deux rotors longitudinaux intègre des volets inférieurs guidant le flux de récolte en fonction de l'inclinaison transversale. Ces équipements s’ouvrent et se ferment pour compenser l’effet du dévers, afin d’uniformiser l’épaisseur du matelas de récolte sur toute la largeur des organes de nettoyage. Le constructeur allemand équipe également ses moissonneuses-batteuses de la fonctionnalité Auto Slope régulant automatiquement la puissance des vents et l’ouverture de la grille inférieure en montée et en descente.
Caisson autonivelant chez Case IH
Les Case IH Axial-Flow de la série 250 profitent d’un caisson autonivelant pour les dévers jusqu’à 12 %, ainsi que de l’automatisme Auto Clean Fan ajustant la vitesse des vents en fonction de l’inclinaison longitudinale. Elles bénéficient également, en option, d’une caméra contrôlant le taux d’impureté et la casse de grain. Les données collectées, couplé à celle provenant d’un capteur mesurant la pression d’air dans le caisson, sont exploitées par le système AFS Harvest Command qui ajuste, en temps réel, les réglages des grilles et du ventilateur. Le caisson intègre également, en bout de la table de préparation, une prégrille envoyant une partie du grain pré-nettoyé directement en trémie. Les Axial-Flow de la série 140 disposent, elles, d’un caisson à simple chute, mais celui-ci adopte une grille supérieure en trois parties autorisant, sur la longueur, trois réglages d’ouverture, pour un criblage plus efficace. La table de préparation, à vis, offre une amenée de matière uniforme sur les grilles, quel que soit la position longitudinale ou latérale de la machine. Cette série bénéficie également du dispositif X-Flow maintenant, en dévers, une épaisseur de récolte constante sur toute la largeur du caisson. Ce système se compose d’un vérin électrique agissant latéralement, afin de générer un mouvement en diagonale des grilles, compensant l’inclinaison latérale de la machine jusqu’à 21 %.
Des tables de récupération de forme complexe sur l’Idéal
Les moissonneuses-batteuses Agco Ideal, à simple rotor (Ideal 7) ou double rotor longitudinal (Ideal 8 et 9), sont disponibles sous les marques Massey Ferguson et Fendt. Elles logent un caisson de nettoyage à double chute (110 et 86 mm de haut), desservi par une table de préparation à mouvement alternatif. Celle-ci est alimentée à son extrémité avant par une table de récupération mobile, en matière plastique et de forme complexe, collectant la récolte provenant du ou des rotors. Ce cheminement de la matière permet d’exploiter pleinement l’action de tri densimétrique sur toute la longueur de la table de préparation. Sur l’Ideal 7, la table de récupération, en une seule partie, réceptionne toute la matière séparée par l’unique rotor. Les Idéal 8 et 9 comptent, elles, deux tables de retour. L’élément avant canalise la récolte sur le centre de la table préparation, tandis que la partie arrière guide le flux sur les côtés. Ce dispositif, dénommé Ideal Balance, permet de préserver les performances dans les dévers jusqu’à 15 %, selon la firme. La compensation de l’inclinaison latérale est aussi assurée par les cloisons présentes sur la table de préparation et la grille supérieure. Cette dernière mesure 2 mètres sur les Ideal 7 et 8 (2,20 mètres sur l’Ideal 9). Sur ces machines, la gestion des ôtons est confiée à un batteur spécifique renvoyant le flux de récolte recyclé sur la table de récupération.