Stress thermique : comment choisir ses ventilateurs pour vaches laitières
En fonction des bâtiments, des besoins et des coûts, plusieurs choix de ventilation mécanique s’offrent aux éleveurs pour faire face aux stress thermiques des vaches laitières : à flux horizontal ou à flux vertical.
En fonction des bâtiments, des besoins et des coûts, plusieurs choix de ventilation mécanique s’offrent aux éleveurs pour faire face aux stress thermiques des vaches laitières : à flux horizontal ou à flux vertical.
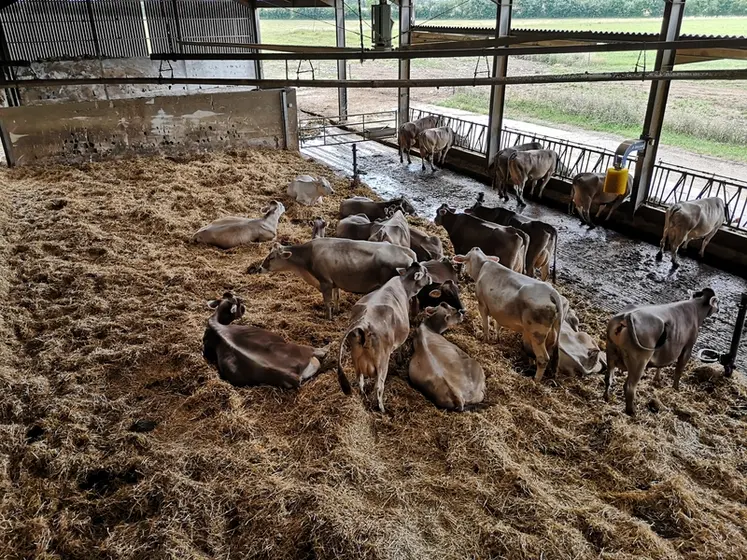
Comment assurer une bonne ventilation mécanique dans les bâtiments pour vaches laitières ? Quand les conseillers sont aussi vendeurs, à qui se fier ? « La pression sur le terrain est énorme, constate Bertrand Fagoo, d’Idele. Des équipements sont vendus sans respect des prérequis ni des priorités. » Alors, pendant deux ans, dans le cadre d’un projet financé par le Cniel, « nous avons mesuré les vitesses d’air dans les étables et rencontré les principaux distributeurs. Ils partagent nos constats mais, entre la distribution et la vente sur le terrain, il peut exister des écarts ». En est sorti un document, rédigé par le Cniel, des chambres d’agriculture, le BTPL et des contrôles laitiers, publié par France terre de lait et édité par le Cniel.
Les ventilateurs boostent la ventilation naturelle
Dans la lutte contre le stress thermique, la première étape est de réduire l’impact du rayonnement et d’améliorer la ventilation naturelle du bâtiment. Ensuite, attention à la mise en œuvre de la ventilation mécanique, qui est un facteur secondaire d’amélioration de la ventilation naturelle. « Ajouter quatre ventilateurs, si on n’ouvre pas le bâtiment, ne résoudra pas les problèmes de ventilation, alerte d’emblée Bertrand Fagoo. Être sous-équipé pendant les périodes de stress thermique peut être pire que de rien n’avoir, car les vaches vont se regrouper sous les ventilateurs. Elles auront moins de circulation d’air sur les flancs, ce qui va générer un stress énorme, avec des risques de blessures. » Il insiste : « avant de brasser l’air, il faut de l’air frais et de l’air sain ».
« Les ventilateurs boostent la ventilation naturelle. Ils créent une légère dépression en faisant entrer de l’air frais, à condition que le bâtiment soit assez ouvert. Pour réduire le stress thermique, ce qui compte, c’est la vitesse d’air sur le flanc des vaches pour faire baisser la température ressentie. Le débit d’air n’est pas le critère essentiel. »
Les ventilateurs à flux horizontal travaillent en relais
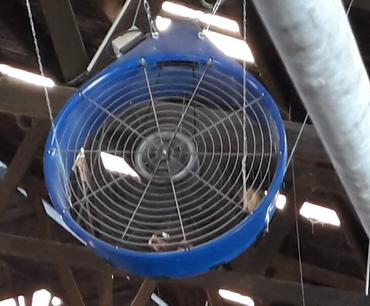
Les ventilateurs à flux horizontal travaillent en relais pour envoyer de l’air sur les animaux. Le premier ventilateur doit être disposé sur le côté est ou nord du bâtiment, à 1,50 m du pignon. Les ventilateurs sont espacés de 12 m en général (15 m maximum). Les matériels de dernière génération et ceux à pales inclinées couvrent 5 à 6 m en largeur, soit deux rangées de logettes face à face, (contre 2 à 2,50 m pour l’ancienne génération) et ont un diamètre de 1,10 à 1,40 m. « Ces ventilateurs tournent très vite, 600 à 1 400 tours par minute, ce qui permet une vitesse d’air d’un mètre par seconde sur les flancs de l’animal. » Les matériels de dernière génération « ont des performances largement améliorées, une consommation électrique moindre et un niveau de bruit réduit ».
• Point de vigilance : la hauteur de pose est conseillée entre 2,70 et 3 m. Il faut donc souvent installer les ventilateurs là où le tracteur n’a pas besoin de passer.
• Consommation d’énergie : 0,5 kWh à 1 KWh quand les ventilateurs tournent à 100 %.
• Bruit : 60 à 75 décibels mesurés.
• Consommation électrique indicative : 100 à plus de 350 €/ventilateur/an selon les situations, la région, l’année et le type de ventilateur.
Les ventilateurs à flux vertical envoient l’air vers le sol
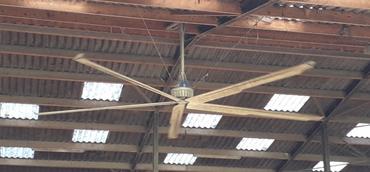
Les ventilateurs à flux vertical « envoient de l’air vers le sol. Pour que l’air ressorte, il faut que le bâtiment soit ouvert sur les côtés », décrit Bertrand Fagoo. Il précise que ce type de ventilation mécanique brasse de grands volumes d’air mais à faible vitesse. Un prérequis est donc l’ouverture du faîtage afin de limiter le risque de faire circuler de l’air vicié. Pour ventiler une aire paillée de 12 m de large sur 72 m de long (soit un bâtiment de 100 vaches), 6 ventilateurs à pales de 6 m de diamètre sont nécessaires, soit un ventilateur tous les 12 m pour obtenir des vitesses de 1 m/s sur les animaux.
• Point de vigilance : il faut une hauteur de bâtiment suffisante, car les ventilateurs sont installés à un minimum de 4 m du sol, les extrémités des pales doivent être à 1,50 m du toit.
• Consommation d’énergie : 0,5 à 1,5 kWh quand les ventilateurs tournent à 100 %.
• Bruit : 60 à 70 décibels mesurés.
• Consommations électriques indicatives : 100 à plus de 350 €/ventilateur/an.
Les installations prioritaires en cas d’arbitrage budgétaire
• Le logement des vaches taries : « Le stress thermique vécu par la mère impacte le veau à naître ainsi que la vie de la génisse sur ses trois premières lactations », assure Bertrand Fagoo.
• L’aire d’attente des vaches laitières : « La densité y est six à sept fois plus importante qu’en bâtiment, la sensation de stress est démultipliée et peut impacter le comportement des vaches : elles iront se coucher sans manger après la traite car elles sont fatiguées », illustre Bertrand Fagoo.
• Les zones de couchage
• L’aire d’accès à l’auge
• Les zones de circulation
Vigilance sur la maintenance
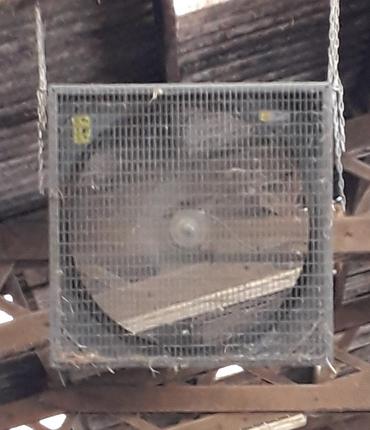
Bertrand Fagoo recommande de dépoussiérer les grilles des ventilateurs au moins une fois par an. Un matériel mal entretenu peut perdre jusqu’à 40 % de rendement et consommera davantage d’électricité, précise le Cniel. « Les variateurs de fréquence, s’ils sont connectés aux ventilateurs, doivent être dépoussiérés. » Les ventilateurs à entraînement direct nécessitent moins de vérifications. Les sondes de pilotage doivent être vérifiées. Si une sonde d’humidité est utilisée, sa valeur peut dériver dans le temps.
Repères
• 5 à 15 °C : c'est la plage de température de confort d’une vache
• 1 m/s minimum : c'est la vitesse nécessaire au niveau des animaux pour réduire la température ressentie
• 5 à 10 % : c'est le nombre d’installations qui respectent l’ensemble des fondamentaux