Dossier - témoignage
L’automatisation selon Nutréa
Le spécialiste de la nutrition animale du Grand Ouest est en train de finir la rénovation des automatismes de ses six usines d’aliments. Avec à la clé des gains très sensibles de productivité.
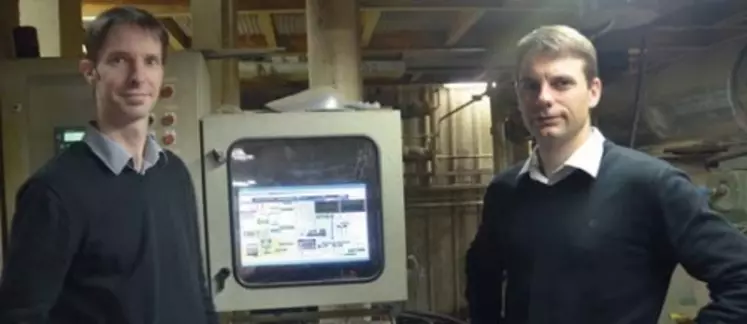
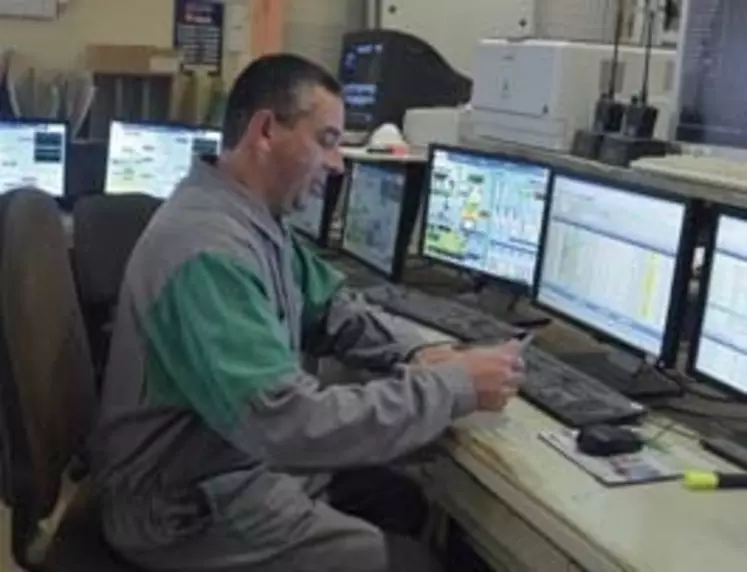
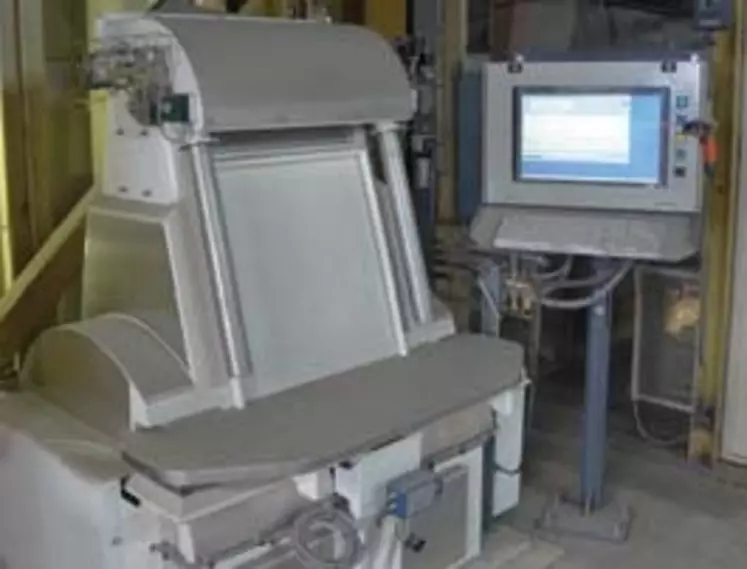
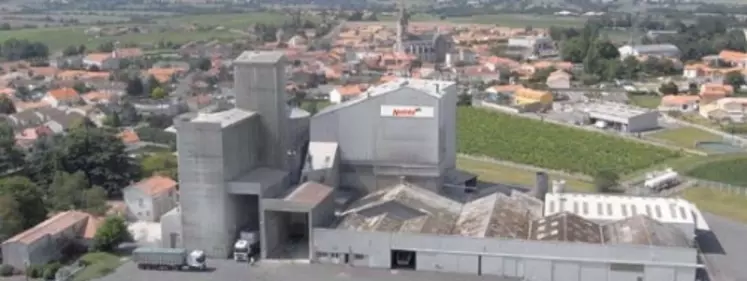
« L’automatisme est une fonction critique pour l’efficacité de l’outil industriel afin qu’il puisse produire à des coûts compétitifs, dans le respect des engagements vis-à-vis des clients. Le niveau d’obsolescence et le faible niveau d’intégration et de couverture d’un système d’information industriel peuvent mettre en défaut une entreprise sur plusieurs points, que ce soit en matière de réglementation ou de productivité », explique Frédéric Guilon, responsable industriel de la Nutrition animale du groupe Nutréa. Dans certains cas, les sites se trouvent même bloqués, y compris en termes d’optimisation mécanique, et ne peuvent qu’avec difficulté prendre en compte, à des coûts raisonnables, les exigences réglementaires de la Drire, de la DSV, ou celles des clients, voire de leur propre maintenance…
« Dans un groupe comme le nôtre, qui possède plusieurs usines très différentes et avec un historique également très spécifique, le projet a réduit l’hétérogénéité. L’offre des fournisseurs et l’état de l’art nous ont permis de nous orienter vers des solutions ouvertes qui nous offrent de meilleures possibilités d’intégration et d’évolution, ainsi qu’une meilleure maîtrise de nos systèmes d’information. » Le bilan est très positif avec, selon les usines, des gains économiques variant de 10 à 25 %. Les gains de productivité s’étagent de 10 à 20 %, les écarts de dosage (hors normes) sont réduits de 50 à 200 %, sans compter les gains de formulation. Plus délicats à chiffrer, ils sont par exemple permis par l’amélioration de la précision des incorporations des matières les plus coûteuses, au plus près des besoins physiologiques de l’animal. « Les gains non financiers en matière de flexibilité et de réactivité sont également incontestables », complète le responsable.
La méthode s’est construite en deux étapes principales : la rédaction des analyses fonctionnelles pour l’ensemble des sites, qui a servi de cahier des charges au fournisseur, puis celle d’analyses fonctionnelles spécifiques à chaque site. « Le système a été construit par Actemium, mais il a été adapté à notre groupe et à chaque usine. »
Landemont, l’ultime site à bénéficier du nouveau système
Le projet de rénovation s’est déployé sur cinq ans, l’usine de Landemont proche d’Ancenis en Maine-et-Loire, étant la dernière à basculer dans son nouveau système, ce printemps 2013. « Nous avons démarré en 2008 avec les usines de Louvigné-du-Désert et de Plouagat, suivies en 2010 par les deux sites de Languidic puis, en 2011, par Plouisy », énumère Frédéric Guilon. L’investissement représente environ 400.000 € par usine pour l’aspect automatisme et son couplage avec l’informatique industriel, plus 250 à 400.000 € pour la refonte nécessaire de la partie électrique afin de pouvoir piloter les nouveaux systèmes. Les autres investissements consentis pour tirer le meilleur intérêt de l’évolution sont variables selon les usines. La mise en place de variateurs de vitesse sur les broyeurs exonère, par exemple, l’usine de changer les grilles lorsqu’elle change de matières premières à broyer. « À Landemont, nous avons par exemple ajouté un verse en sac pour les médicamenteux car l’automatisme peut désormais les prendre aussi en charge », illustre Olivier De Hoest, responsable du site. L’automatisme est en effet désormais capable de gérer les interdictions dans les successions de lots contenant des médicamenteux. Toutes les contraintes sont coordonnées par le progiciel de gestion intégrée (ERP), ce qui confère une sécurité de plus aux opérateurs. Il en est de même pour l’obligation d’un second tamisage pour les aliments Lapin ou pour l’enrobage des aliments de finition Dinde.
Construit en 1973, dans la grande période de développement des usines d’aliments pour animaux françaises, le site de Landemont a été agrandi à plusieurs reprises. « L’usine était donc déjà très bien automatisée, au contraire par exemple de Plouisy, où l’automatisation de la granulation a fait gagner 25 % en productivité. Nous conservons donc un fond très similaire au précédent, avec quelques options de plus et des interfaces bien plus conviviales, puisque nous abandonnons l’ancien synopsis au profit d’écrans en salle de contrôle comme dans l’usine. Le progiciel est très intuitif. Notre équipe, qui était déjà bien au point, suit au total une formation sur poste de trois à quatre jours ». L’important c’est que l’opérateur se sente toujours bien le pilote de l’usine. Mais le gain de temps est central pour la productivité : l’analyse fonctionnelle permet toujours une remise à plat des procédures, ce qui constitue en soit une première étape vers l’optimisation.
Enfin, la remontée automatique des informations vers le système central s’effectue plus rapidement, et sans erreur de re-saisie, pour une meilleure gestion globale des sites, rendant possible une optimisation de l’affectation des productions selon les sites.