Aux Pays Bas, Willy van Erp est plus serein en poulet Beter Leven
Depuis plus de quinze ans, Willy van Erp produit du poulet répondant au cahier des charges Beter Leven 1 étoile (BL1*), bientôt obligatoire aux Pays- Bas. Sans regret.
Depuis plus de quinze ans, Willy van Erp produit du poulet répondant au cahier des charges Beter Leven 1 étoile (BL1*), bientôt obligatoire aux Pays- Bas. Sans regret.
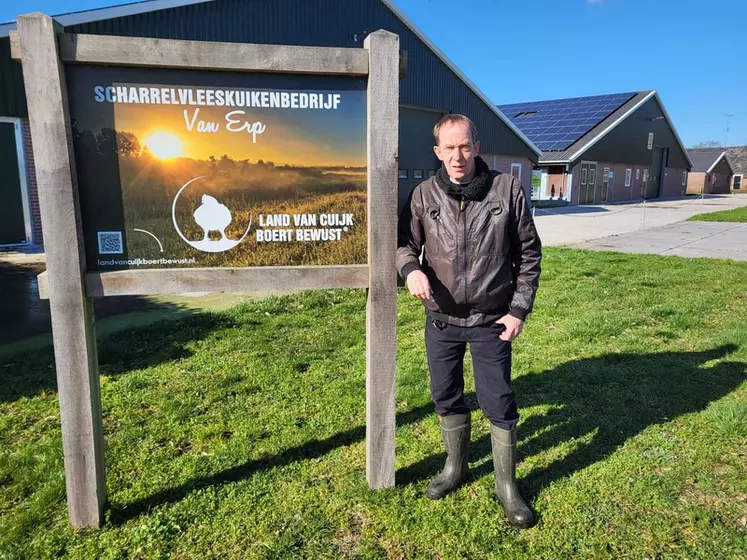
« Je ne connais pas un seul éleveur converti au Beter Leven une étoile (BL1*) qui soit retourné en conventionnel. » Le constat de Willy van Erp en dit plus qu’un long discours. L’éleveur est un pionnier du poulet BL1* aux Pays-Bas.
En 2006, il change son fusil d’épaule en diminuant de moitié la densité de l’atelier de poulets de chair démarré en 1970 par son père. Au lieu de 20 000 oiseaux engraissés en 42 jours, il passe à des lots de 12 000, prêts en 56 jours.
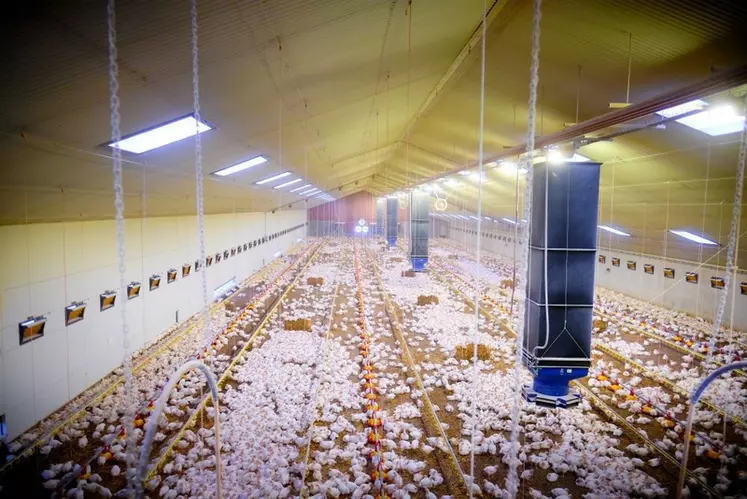
« La demande portait sur de plus petits ateliers. Je me suis lancé car j’ai cru à ce système. Je me suis dit que la conduite d’élevage serait plus simple avec moins de main-d’œuvre et de nettoyage. Je m’attendais à ce que ce soit un marché de niche pour une petite frange de consommateurs prêts à payer un peu plus cher. Mais je me suis trompé ! La demande de la grande distribution ne porte plus que sur ce type de poulet ! », explique-t-il.
En 2008, il arrête son troupeau de 75 vaches laitières pour se consacrer à 100 % au poulet. Puis, en 2013, il construit un second bâtiment de 2 140 m² jardin d’hiver compris. Un troisième, identique de 20 000 places, suit en 2017. Au total, l’élevage dispose de 52 000 places.
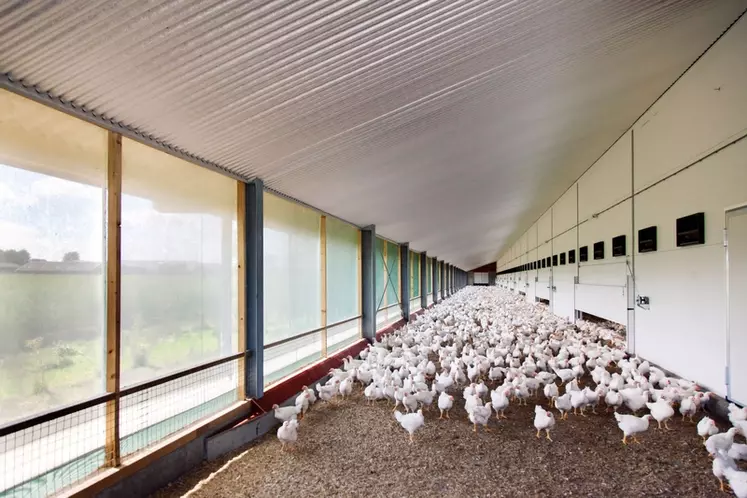
Ils fonctionnent avec une ventilation en dépression pendant les trois premières semaines d’élevage. « La pression constante conviendrait mieux pour réguler la température, mais son installation est plus complexe et son coût plus élevé », remarque Willy.
Du blé pour piloter le poids d’abattage
En poulet bien-être une étoile, « tout est un peu plus simple. Mais cela ne signifie pas que les bons résultats techniques suivent automatiquement », prévient Willy, installé sur 30 hectares à Sint-Anthonis près de Nimègue, dans le Brabant. À l’arrivée des poussins JA 757 Hubbard, les bâtiments sont chauffés à 35 °C. La température est abaissée à 23 °C à partir de trois semaines. Dans les deux bâtiments les plus récents, des récupérateurs de chaleur permettent de réduire de 20 à 30 % la consommation de gaz.
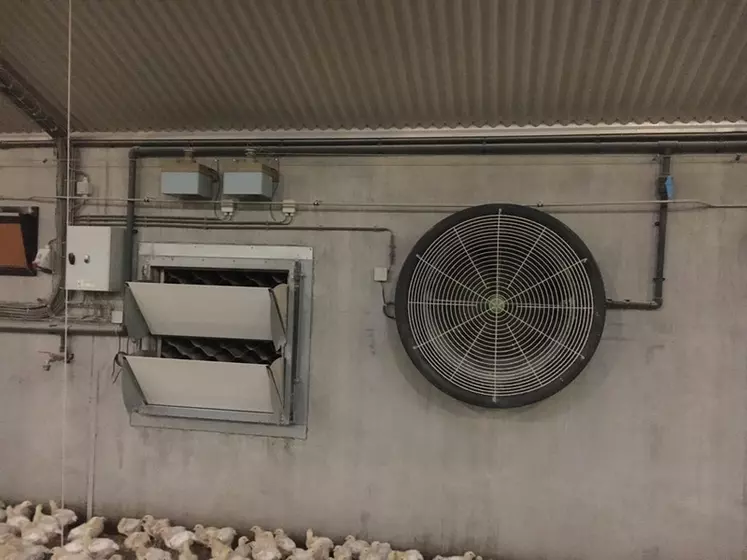
Willy vaccine de manière classique contre la bronchite infectieuse, la maladie de Gumboro, la maladie de Newcastle, mais pas, comme la plupart de ses collègues, contre la maladie de Marek qui lui cause peu de souci.
L’alimentation avec une ration moins riche en énergie et en protéines demande un pilotage précis. « Je distribue une formule standard dont je peux remplacer 15 à 20 % par du blé. Ce blé additionnel constitue ma marge de manœuvre. Je diminue la part d’énergie. C’est un moyen de rester entre 2,4 et 2,5 kg à l’enlèvement et ne pas les livrer trop lourds auquel cas je suis pénalisé de 2 centimes/kg. Mon IC augmente mais je gagne un peu sur le prix de l’aliment. » L’Indice de consommation oscille ainsi entre 1,98 et 2, la mortalité entre 1 et 1,5 %.
Des poulets plus actifs
Les animaux ont accès au jardin d’hiver par des trappes de cinq mètres de long. Elles sont plus simples à installer qu’une version d’un mètre et leur envergure facilitent la fluidité de passage. Willy manie les trappes manuellement. « C’est un peu de travail en plus. Mais je préfère. Un système automatique risque de laisser des animaux dehors à la fermeture », justifie-t-il.
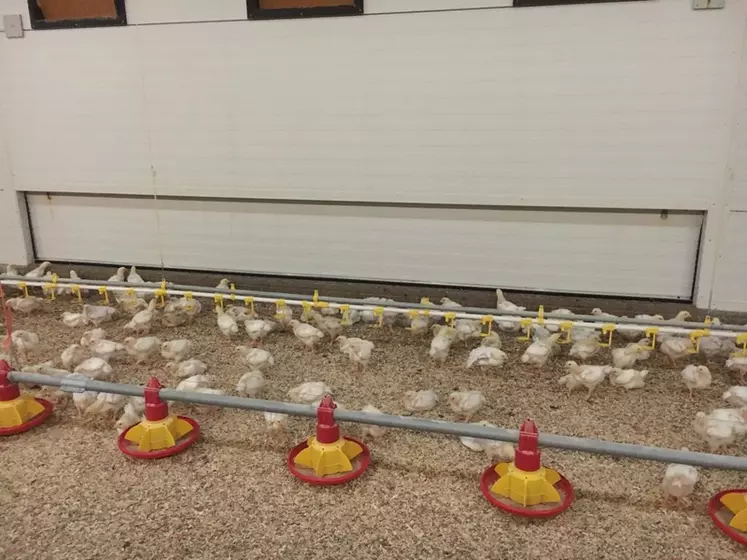
La conduite demande des aménagements. « Les poulets sont plus actifs. Ils sautent sur les lignes de distribution de l’aliment. C’est problématique en finition quand ils sont le plus lourds. J’ai donc tendu deux fils par-dessus pour les dissuader de s’y percher », signale Willy.
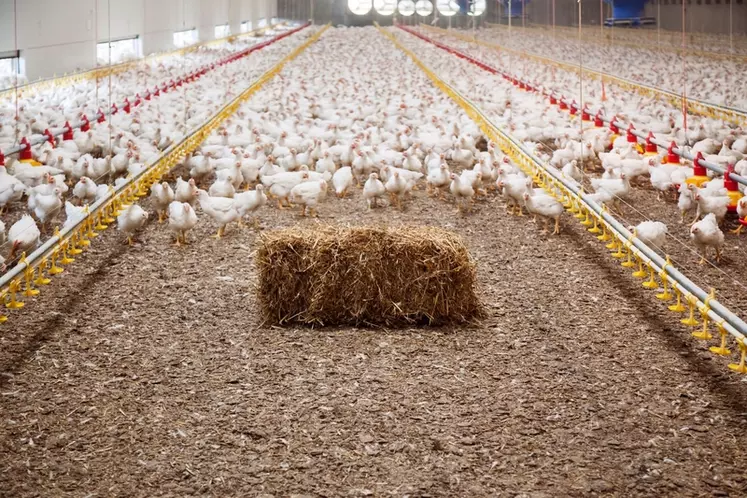
La surveillance est un autre point clé. « Je passe trois à quatre fois par jour pour vérifier l’ambiance, observer la répartition des animaux, leur comportement au jardin d’hiver. L’atelier me demande en moyenne trois heures par jour. Je confie le nettoyage à un prestataire. C’est une autre conduite. Mais je suis plus serein. Je ne regrette pas mon choix », résume Willy. « Comme la litière est plus sèche, les poulets ont moins de pododermatites. Je n’ai eu que rarement besoin d’antibiotiques. Tout au plus quatre à cinq fois depuis 2006. »
Garantie du débouché contractualisé
L’éleveur se sent d’autant mieux qu’il dispose d’une visibilité économique. En 2010, il a signé son premier contrat de cinq ans avec l’abatteur Plukon, lui-même engagé pour fournir l’enseigne de la grande distribution Albert Heijn.
« J’ai la garantie du débouché. J’ai le choix entre deux accouveurs et cinq fabricants d’aliment et je suis lié à mon acheteur. Contrairement à certains de mes collègues, ce n’est pas un problème pour moi. Le prix de reprise est calé sur une formule qui tient compte des prix de l’aliment, de l’énergie, de la litière, du ramassage… La révision des charges variables est prévue deux fois par an », précise Willy qui se déclare satisfait du bilan économique de ses quinze dernières années. « Je n’ai pas toujours profité des prix élevés du marché, mais je n’ai pas non plus subi les prix les plus faibles. Je touche un prix plus constant, correct, en moyenne 1,45 euro/kg vif, 40 centimes de plus qu’un élevage conventionnel. »
Rendre l’élevage « plus attractif »
À 61 ans, Willy van Erp a toujours des projets, ne serait-ce que pour transmettre son exploitation.
Les éleveurs engagés en BL1* ont pris des engagements climatiques et environnementaux à court terme. Pour sa part, Willy a déjà posé plus de 3 000 m² de panneaux solaires. Il va investir 16 000 euros par bâtiment dans un système d’ionisation qui agglomérera les poussières sur un fil tendu au plafond.
Une fois le bâtiment vide, il coupe l’électricité et le résidu tombe au sol. « En BL1*, le taux de poussières est plus important en raison d’une ambiance plus sèche et de l’activité supplémentaire des poulets. Avec ce système, il devrait baisser de moitié », avance Willy. L’équipement est subventionné à 60 % par les pouvoirs publics et la facture d’achat a été réduite de 30 % grâce à une commande groupée par huit ateliers.
Sésame du permis de construire
Avec deux fils n’ayant pas l’intention de reprendre l’exploitation, Willy n’entend pas rester pour autant l’arme au pied. Il envisage de rajouter un bâtiment, voire deux, pour rendre l’élevage « plus attractif » à des repreneurs. Sa ferme dispose encore d’un quota azote et phosphore, hérité de son ancien troupeau laitier.
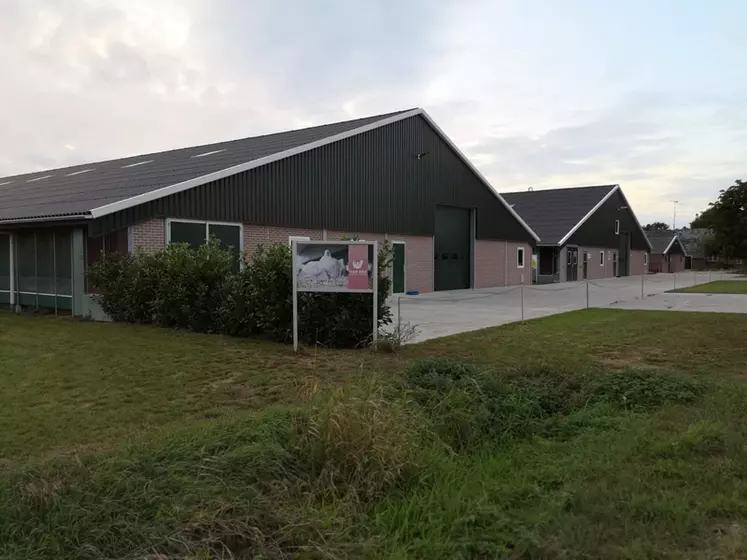
« Il devrait être transposable en poulet », commente Willy. Avant, il lui faudra obtenir le sésame du permis de construire. « Cela peut prendre plusieurs années… » Et puis il y a la hausse du coût des matériaux et de la main-d’œuvre. La Covid a propulsé l’investissement de 200 à 300 euros du mètre carré. La guerre en Ukraine l’a porté à 400 euros du mètre carré. Willy n’a pas encore tranché car tout cela lui fait « un peu peur »…